For no other reason than that a gyro was in the process of being fitted to a 16.8m Maritimo cruiser during a recent visit to the Maritimo manufacturing facility in the Gold Coast Marine Precinct – I decided there and then to investigate for myself the pros and cons of this ‘stabilising’ medium.
There has been a lot of ‘talk’ of late, and I wanted to get the facts for myself, one way or the other. The brand name of this particular gyro product was Seakeeper and I have to admit to not having ever heard of this company before. Nor, incidentally had local power transmission specialist Twin Disc Australia ever heard of it,for it apparently took Twin Disc two years of research before its investigations led it to the door of Seakeeper. “The most important attribute was that it was all internal, negating the need to fit any ‘appendages’ to the outside of the hull,” Twin Disc development manager Trevor Tucker explained. “It could be for a new boat or indeed a decidedly easier retrofit on an existing model. It was a perfect fit for our range of propulsion and boat-handling products!”
While Maritimo has seemingly embraced the technology and is in fact already up to boat four, (with others still in the pipeline), the reality is that having located a suitable product, the biggest hurdle for Twin Disc has been convincing other boat manufacturers in our South Pacific region, of the merits of this particular form of stabilisation. Innuendo and a resultant lack of understanding abounded and I must confess it gathered me in also, until that is I learned that Maritimo had fitted not one but four systems already. Then I began to get suspicious, inquisitive.
As most everyone in the Australian marine industry will attest to, the hardest man to ever convince when it comes to new products or concepts would have to be Maritimo supremo Bill Barry-Cotter. He has a big reputation to uphold, along with a duty to his clients to adorn his Maritimo cruisers with only the very best equipment available at the time. He will not waiver from that commitment – until he is well convinced of the merits of any new proposal or product.
Okay, initially it was on the insistence of an American client who already knew of gyros and therefore endorsed the merits of this form of stabilisation, but for Barry-Cotter to embrace the concept firstly by allowing it to happen, and secondly to then fit them on subsequent vessels – got me to thinking – maybe, just maybe all the innuendo associated with this gyro system is just that, ill-found negatives from people with different (hidden) agendas!
What is a Gyro?
Gyros are not new, the technology having been around for decades in submarines, space shuttles and most aircraft. The humble child’s spinning top is another version of a gyroscopic force in action also, but companies such as Seakeeper have taken the concept one step further again and perfected the concept for marine application. The secret to its success in this environment is in the partial vacuum (to almost eliminate air resistance) the flywheel spins in!
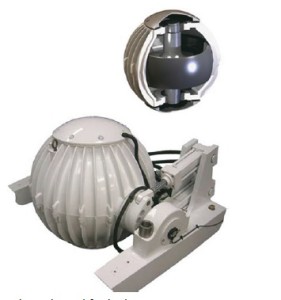
The Seakeeper gyro consists of a massive precisely-engineered 250kg steel flywheel which runs in a partial helium vacuum, inside an aluminium sphere, or dome. This flywheel spins on a horizontal plane at 9,700rpm and in simple ‘layman’s terms’ this spinning action which generates 7,000 kilogram metre squared per second of angular momentum, instantaneously creates a stabilising torque to oppose any rolling motion imposed on the vessel by wave action.
The greater the figure in each case, the more effective a gyro is, but at the same time this gyro can be equally as effective if you have less weight, spinning at a greater speed. But then of course a whole lot of other influences enter the equation, so in the end you come back to Seakeeper’s design parameters set down for these particular gyros, when used in marine application.
In short then, when your boat starts to pitch or roll in a sea, this flywheel spinning on its axis within this gyro, instantaneously creates torque on its mountings to oppose the pitching or rolling, or both at once. As it does so, this sphere which is ‘managed’ by motion sensors and computer micro-processors, will ‘precess’ or in effect autonomously roll on its gimbal bearings – in direct response to the corresponding degree of the roll of the boat.
It is on the go the whole time for the amount it moves in order to counteract the motion of the waves, is entirely relevant to the resultant angle of the boat. Or put another way again, this stabilising force emanating from within this sphere, will in effect push one side down, and the opposite side up. One ‘convinced’ pundit recently summed it up rather eloquently by suggesting the sensation was akin to a great big hand reaching down from the sky, grabbing the boat and literally suspending it at a level attitude.
Some people have the mistaken impression that this system is supposed to somehow stop all boat motions – up, down, bow to stern, regardless of the sea conditions. Arguably that could also be described as emotive innuendo for of course there is no way in the world it or any other stabilising system for that matter will hold the boat absolutely still; what it does is reduce the gunwale to gunwale rolling, so the boat remains as level as possible – throughout the action of the wave. The larger the wave, the bigger the roll, the more the gyro kicks into action with its pre-programmed counter moves that allow the boat to rise and fall sure, while at the same time dramatically reducing rolling and pitching
Installing a Gyro
The whole gyro assembly comes as a complete package inclusive of cooling hoses, control boxes, wiring loom and the substantial aluminium cradle it all fits onto. Great care must be taken with the mounting of this cradle, for it needs to be mounted securely so it doesn’t come adrift or ‘chatter’ in years to come. Twin Disc has a dummy cradle they lend to boat manufacturers, so the bed can be built to ‘precisely’ fit this cradle. Once the ‘top-hat-section’ GRP bed is built, sanded and then finished in gelcoat (other of course than the actual area where cradle meets bed), the two are ready to ‘marry and remain faithfully together for ever after’.
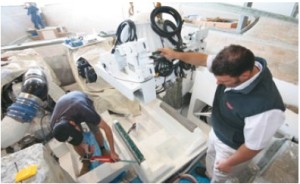
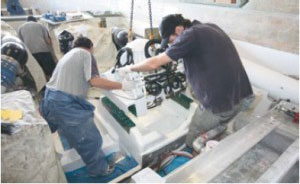
A very top end adhesive is used to attach this cradle to the bed – it is not bolted – so the gap between bed and frame must be of a pre-prescribed tolerance. Cleanliness is a very big issue right the way through, when setting this up for attachment to the bed, so every effort is made to ensure the surface of your cradle as well as the surface of the bed is completely devoid of dust or any foreign matter that could react with the adhesive , or indeed create air bubbles.
Once both surfaces are properly prepared it is simply a matter of applying this special two-pot adhesive (that is of a paste consistency) to both surfaces using a plastic spreader, then activating the overhead crane and judiciously lowering the complete gyro assembly onto the bed. Somewhat of a messy job, the weight of this assembly ensures the adhesive oozes out for a good 3-4 hours after initial contact, so that excess needs to be cleaned up on the run so to speak.
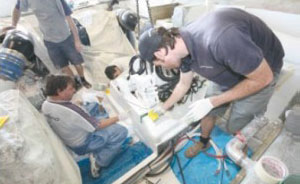
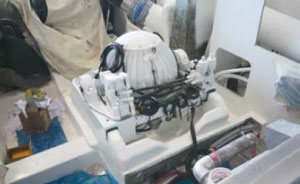
Following this it is then a matter of waiting a day or so (it takes a minimum 10 hours) for the adhesive to cure, whereupon the AC and DC control panels and all the electrical, hydraulic and plumbing peripherals can be attached. It really is as simple as that!
The Seakeeper Gyro In Action
A rarity I know (not), but the Gold Coast was suffering the effects of a rousing storm – perfect conditions to run our Maritimo 550 down the bay, out the Seaway and off into some genuine bluewater conditions. As per predictions our Seakeeper gyro took 35 minutes to reach its terminal velocity of 9,700 rpm. In the cabin you couldn’t hear it going, upstairs on the flybridge level you definitely couldn’t hear it going. That part was fine!
The digital read-out and touch-pad on the dash allowed the gyro to be activated when it had reached the unlocked minimum operating speed of 7000rpm, but we decided to let it wind right out to 9,700rpm – so we would feel the optimum effects of the system. Interestingly, on our way out I checked the power consumption also, for I wanted to be sure in my own mind that what I was quoting was accurate!
This read-out, while surprisingly small and unobtrusive, in actual fact offered a plethora of information within its menu, monitoring such facets as boat roll angle, rpm, bearing temperatures, motor temperatures, control box temperatures, vacuum pressure, fault diagnosis and of course current draw.
Current draw was particularly illuminating, for while in initial build-up to its operating revs it was drawing 12 amps, it reduced as the speed ramped up for it was drawing 8.5 amps at 8000rpm and just 3 amps when it reached its optimum speed of 9700rpm. We stopped our 30 tonnes of Maritimo 550 Flybridge beam on in the roughest part of the Seaway entry and whilst still in ‘lock’ mode we were rolling through a 120-degree axis, rolling 60 degrees one way, then back 60 degrees the other way (more in fact). Pressing the ‘Sea’ button, after just one familiarisation wave I could feel this “big hand coming out of the sky, reaching down and holding the boat steady”.
It was a ‘feeling’ that was very hard to put into words as it was sort of like a big shock absorber in action, for as soon as it begins the roll you can feel the gyro take over and allow it to come back to a level attitude – without rebounding to fall over on the opposite side of the roll. It was a most uncanny feeling; you brace yourself for something you think will happen under normal circumstances, and it gets half way through the movement then it goes sort of doughy (suspended) and the roll is halted.
Under power the characteristics were again most enlightening, for our Maritimo held a level attitude when we threw her into a tight turn at 20 knots. Who said the system didn’t work at speed? There was a feeling of security too when at a trolling speed of 6-8 knots, it held the boat level right through the full 360° of what was a very messy swell with waves on top.
Certainly that was a biggie for anyone who is susceptible to sea-sickness; the other point worth mentioning was the realization that at speed it was a hell of a lot easier to steer. That was somewhat of a surprise both to myself and to Aaron, our Maritimo skipper, for it was virtually hands free running at three quarters into the sea and in a following sea. To me that graphically proved there was some sort of ‘force’ in action. Before engaging the gyro, we needed 15-degrees of rudder each way, but after engaging the system, it was hands-free!
The final surprise for me came at the end of the test when I learned that while the system takes 35-40 minutes to ramp up to 9,700rpm, such is the quality of the bearings and the free-wheeling friction-free ease with which the flywheel spins – it then takes a whopping four hours for it to wind down again. Surely that is confirmation of Seakeeper’s claims that only the very best components (in this case friction-free bearings) have been used, from leading manufacturers worldwide.
Myths Department
Undeniably, the system works and works damned well, and it is certainly not hard to appreciate why leading brands such Azimut, Sunseeker, Fairline, Princess, Ferretti, Maritimo, Riviera, Marlow, Carver, Ocean Alexander, Viking, and Pershing – have all embraced the concept and are fitting Seakeeper gyros to their boats. But there are always knockers for one reason or another and certainly through my investigations I heard some real whoppers; by and large myths that bear no resemblance whatsoever to reality. Here are just some of them – with my thoughts on each point:
Gyros Use Heaps of Power.
I will kick this segment off with this one, for this is perhaps the biggest fallacy associated with the concept. In the early days gyros were probably on a par with fins but as in any situation technology ensures things can only get better, with the net result that today gyros use less power! This system draws just 3kW of power to get the unit up to full speed, and 1.5kW once it has reached that speed. Compare that to fin systems, which can use anything from 10kW to 21kW of power to keep them operational.
You Need to Run a Generator Dedicated Solely to Powering Up Your Gyro.
This goes hand in hand with the above. You do not need anything other than the battery bank/inverter/charger/genset specification you would typically run on your size of cruiser.
Gyros Cost Way More than a Set of Stabilisers.
Comparing unit for unit, yes the gyro is marginally more expensive at just on $100,000. Compare the cost of installation, compare the cost of a cradle-bed versus cutting holes in the side of your boat and fitting hydraulics and appendages each side, compare the cost of on-going maintenance, compare the on-going power costs – the gyro comes out way ahead!
Gyros Make a Lot of Noise, and they Vibrate a Lot.
A gyro is a precision instrument so there is no allowance for even the slightest amount of vibration. Underway, the gyro was quieter than the genset; I know because we stopped and started each one, individually.
Some armchair critics suggest a gyro will only work at rest or slow idle; still others suggest it will only work over a certain speed.
Both are wrong for the very real plus of this system is, it will work at speed, and it will work when you are moored in a secluded bay that is being churned up by inconsiderate boaters travelling too fast. It’s relatively quiet (way quieter than a genset for instance) operation enables the skipper to run the gyro all night if need be.
The system won’t work on a smaller boat, or conversely for that matter, a larger boat.
The system will work in any vessel that can handle an additional payload of 455kg. The Seakeeper M7000 system will suffice for a vessel up to 30-35 tonnes, which traditionally is up to say 17m. Over that size you can fit multiple systems (there is a strict formula and criteria Twin Disc works by) or indeed fit a new M21000 (half the weight of three M7000 models) model which will handle vessels up to 90-tonnes. There is a system for every boat and every situation, be it commercial or recreational!
It takes a long time to warm up.
It doesn’t actually have to warm up, merely it is coming up to it gyroscopic rpm speed, to where it is most efficient. During my test of the system the Seakeeper took approximately 35 minutes to reach terminal velocity, which in the context of our leaving the Maritimo base and heading off down the Broadwater for our 45-minute trip to open waters – was absolutely no imposition or inconvenience, whatsoever.
You have to re-start it every time you want to use it, when at sea.
Wrong! Once up and running it is simply a matter of pressing the lock button beside the Seakeeper digital read-out on your dash, and activating or de-activating the gimbal brake. This locks the sphere in place and while allowing the system to continue running at the existing rpm, its gyroscopic powers are isolated/removed – because it can’t roll to the motion of the boat! It is that simple; at the touch of a ‘lock’ or ‘sea’ button you can virtually instantaneously activate or de-activate the system.
They are hard to fit; more importantly costly to fit, especially in a retro situation.
Nothing could be further from the truth. All you need is somewhere solid to mount the assembly, which in a retro situation will most likely require the adhesive bonding of two beds or ‘bearers’, into the bottom of your boat. Otherwise, some electrical work, fit the plumbing and coolers – and you are back on the level. The very real plus of this system is that you DO NOT need to fit anything outside the confines of the hull, for there are no holes cut in your boat, and no exterior appendages involved. That, as you can well appreciate folks, is a godsend for you can pull up to a marina or wharf, without fear of damaging or indeed breaking off, any exterior fins/peripherals.
A gyro won’t control the fore and aft pitching you get in the bigger seas.
No, indeed it won’t control that motion; in fact no stabilising device available on the market today, will control that phenomenon. They are not designed to, for those are totally different and virtually uncontrollable forces that seemingly just can’t be tamed.
Gyros take up a lot of space.
If you consider a width of 977mm, a length of 778mm and a height of 671mm, to be a lot of space, then yes I guess it does. The truth is it takes up very little (underfloor) space.
There isn’t much room in the average engine bay, to fit a gyro.
In some cases true, but often irrelevant, for the gyro system can be fitted anywhere in a cruiser – as long as it is aft of the amidships line. It can be off to either side, too, and it doesn’t have to be mounted on the centreline.
Gyros can only be fitted to a new boat.
No, they can be retro-fitted to any boat, so long as you have the room available, and a solid mounting point.
They have to be serviced at very regular intervals.
The Seakeeper gyro requires only very minimal servicing – every two years or so it is primarily a visual inspection of the electrical systems, the cooling devices and the hydraulic hoses. Internally the system runs in a virtual vacuum which is partially back-filled with helium, so there is no potential for corrosion, and the bearings are ceramic versions as used in the landing wheels of Boeing 747 jumbo jets. Really, little can go wrong but in the event that something does, your digital diagnostic read-out on the dash will advise you accordingly. And if the particular problem is too bad, then the system will shut down completely!
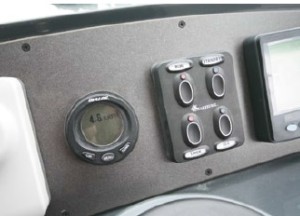
Once you have fitted a gyro, that’s it, and you are stuck with it, for you can’t get them out again.
Rubbish. The dome and peripherals come apart from the actual cradle. At worst you could leave the cradle attached to the beds you fitted; at best you just get a side-grinder into action and cut the beds off at hull level, sand it all up, flow-coat it and you would never ever know one had been fitted in the first place. The reality though is you wouldn’t want to get rid of it anyway, so effective is its operation.