TESTING FOR SAFETY AND RELIABILITY AT SEA
In late November, we had the privilege of being invited to witness Gurit’s impact testing for Corecell™ M & S foam at the Auckland University, Centre for Advanced Materials Manufacturing and Design Testing Laboratory.
The Gurit Engineering team operates its own testing laboratory at their North Auckland facility and has worked closely for over 25 years with the Auckland University Testing Laboratories in Newmarket, Auckland on research and development for marine applications.
During the visit, we observed the testing of Gurits Corecell™ as used in locally-built Kiwi vessels, such as:
• Stimson Marine Design Origami 530 Optimistic, featuring a single-skin bottom and Corecell™ topsides.
• Amphibious tender for the superyacht The Beast, Corecell™ throughout.
• Yachting Developments’ Sportsfisher 40m, Lanakai.
• Lloyd Stevenson Catalyst yacht tenders
• Nic De Mey 60 Spaceship (as featured in our last issue).
• Elite 22m Flybridge Motor yacht currently in build at Weber Marine (as pictured below).
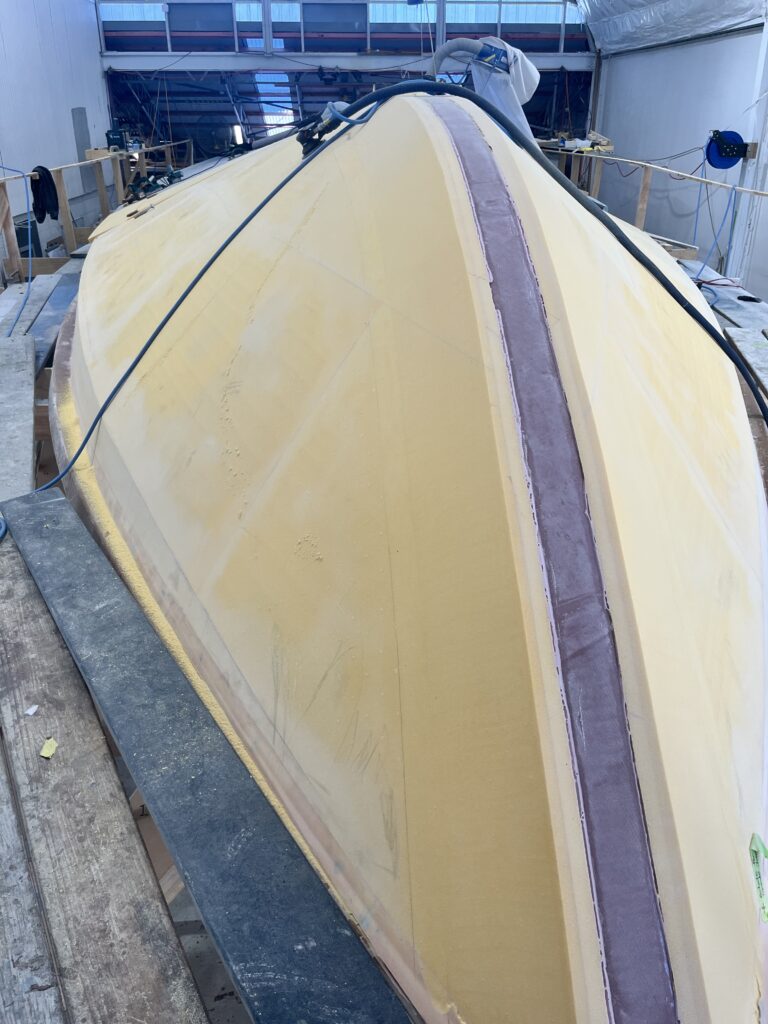
At the former Lion Breweries site (where, notably, not a drop of beer remains), we were first shown the large Servo-hydraulic Slam Testing System (SSTS), 14,500L Water test tank. Here, Gurit products are equipped with stress monitors and subjected to forceful impacts by being dropped into the tank, simulating the forces a hull might experience when striking waves at various speeds. This enormous test rig, developed in 2005, is located in the basement, where it can carry out these violent tests without disturbing the other labs.
Gurit often uses an alternative impact test method, also at the Auckland Uni Lab, that uses a small and faster test. This smaller scale test was developed by a Gurit-sponsored Masters student and has enabled a greater range of projects to benefit from the toughness and reliability evaluation, including the IMOCA60’s and also commercial vessels like ‘ Ika Rere’ Wellington’s electric ferry, Emirates Team New Zealand’s Chase Zero to the 40m ferry fleet for Hong Kong.
We then moved to the main test lab, where Gurit’s Corecell™ structural foam was under going evaluation in the universities instrumented drop tower. This process is used in conjunction with Gurit’s own in house 6m drop tower, fitted with a 16kg sharp and blunt impactors, capable of delivering impact energy of 900J. This testing is used to evaluate the toughness of hull designs, by simulating both water slamming and debris impact.
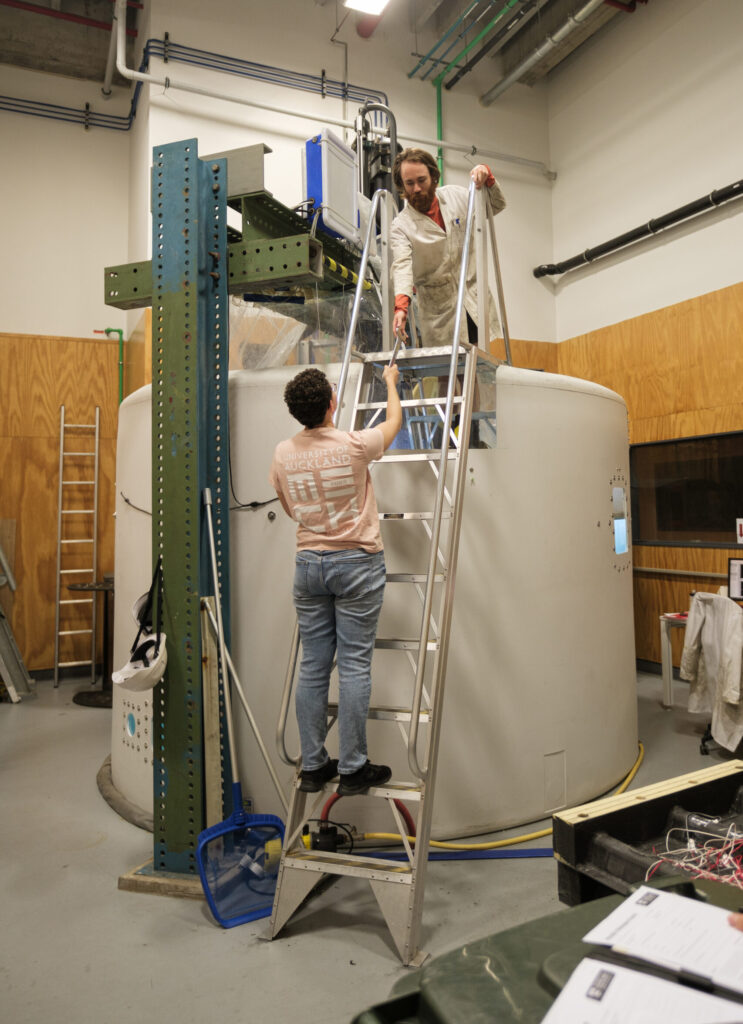
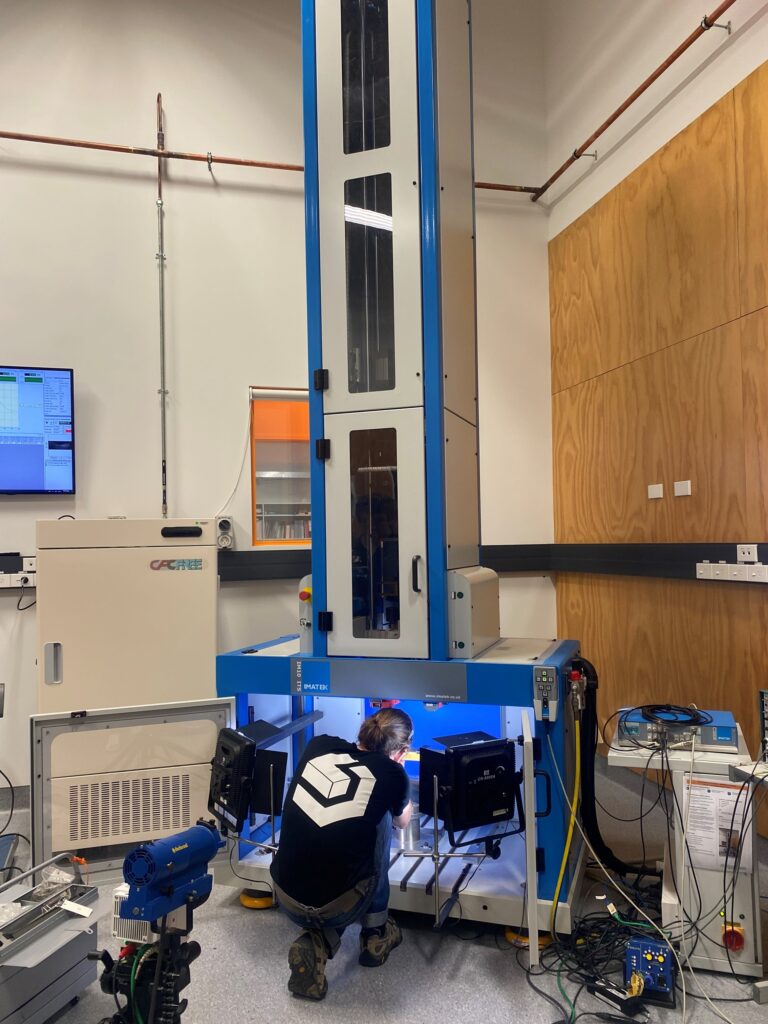

We were impressed by the product’s flexibility during testing. A simulation of debris impact at approximately 40 knots showed that while the foam core was compromised, the Corecell™ product rebounded into shape with its outer layer remaining watertight. In many cases, this should allow vessels to return home for repairs safely. By contrast, similar tests on aluminium resulted in punctures resembling bullet holes from a high-powered rifle. The lighter Corecell™ product’s resilience to impact was impressive, particularly for boat builders seeking lightweight materials without sacrificing strength.
The testing at Auckland University and Gurit Asia Pacific’s accredited mechanical testing lab is held in such high regard that Gurit’s Canadian manufacturing facility frequently sends materials to New Zealand for evaluation. This collaboration between industry and our Universities is a testament to the skill and expertise of the New Zealand team. After witnessing these tests, I felt a newfound confidence in the strength of Gurit’s modern hull materials. Knowing their ability to withstand substantial impacts – such as collisions with submerged logs or containers – offering peace of mind when venturing out to sea. In addition to improved slamming performance and increased safety, these materials provide greater durability and longevity, bringing a high performance and lightweight approach to marine construction.
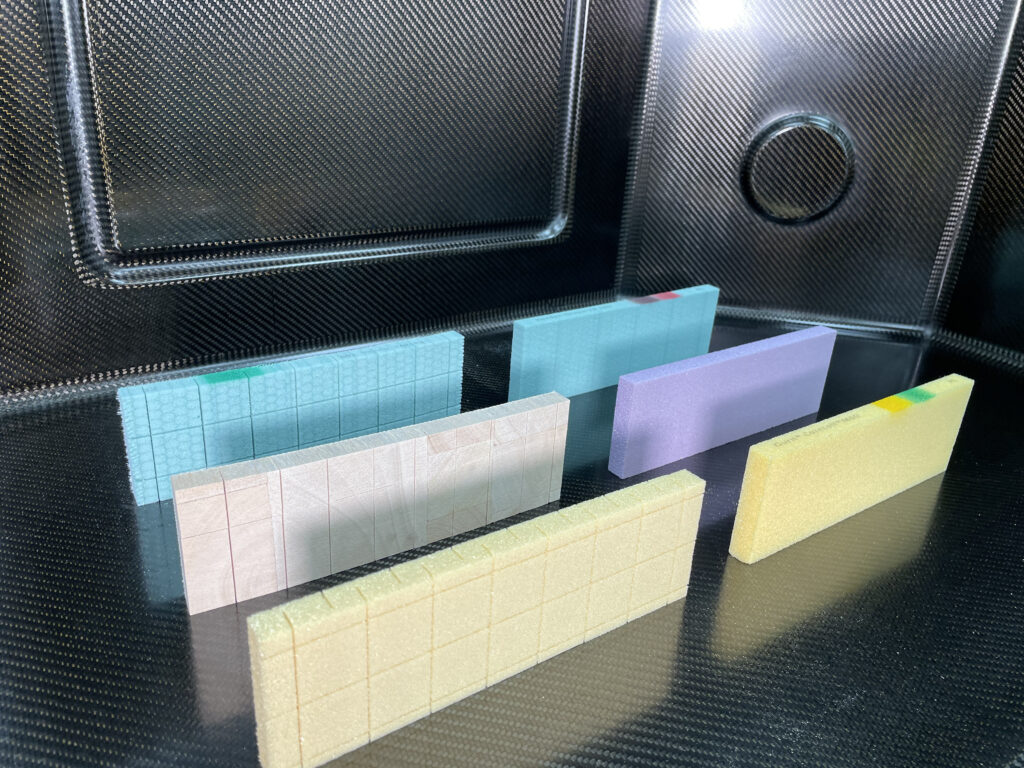
Well done, Gurit! It’s no surprise that the company is a leader in composites, continually advancing quality, strength, and sustainability in its products.
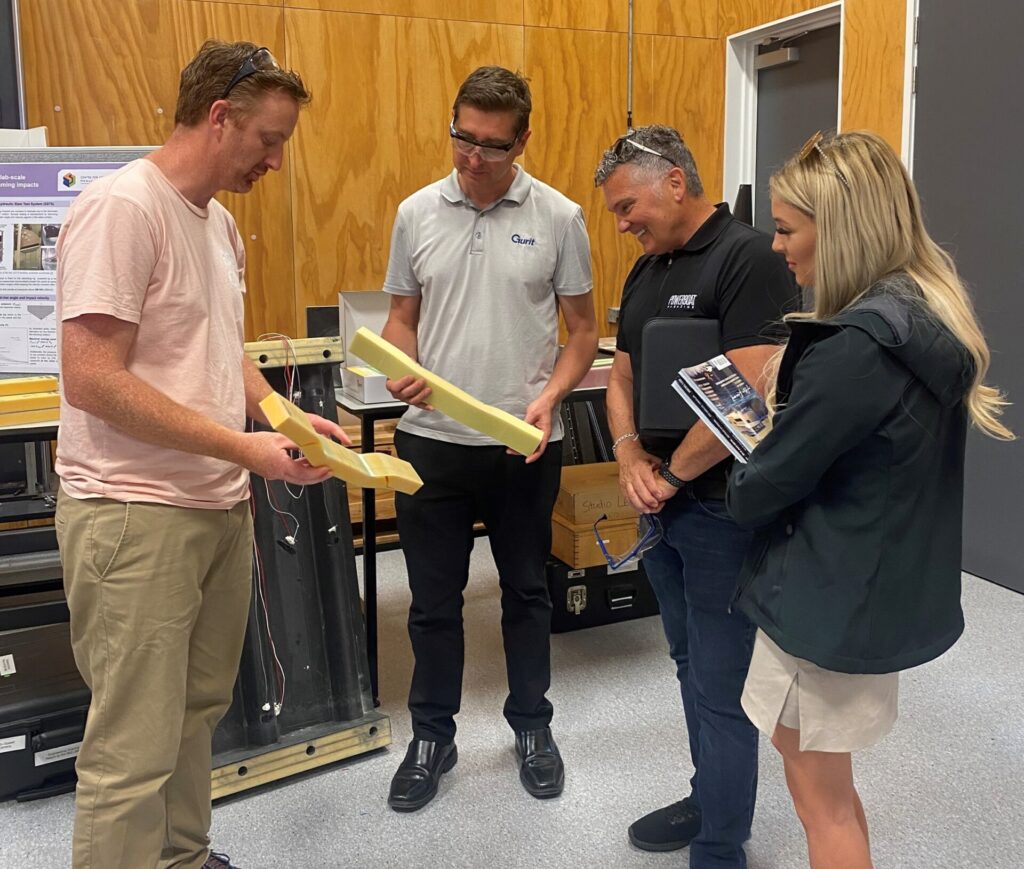