of the boat that can then be unrolled onto flat panels for cutting. b; CNC machines capable of cutting out these parts as accurately as they have been drawn. And c; the advancement of better and cheaper welding machines.
Gone are the days of designers drawing on film using ducks and splines to loft lines. Most designers these days would be designing boats on computers. While drawing on computers is not as enjoyable as lofting pencil lines on paper, the reality is that the information, which can be generated from a 3D digital model far, exceeds what can be pulled off a 2d pencil drawing and builders demand and indeed expect this level of information these days.
It is the combination of these three things that has opened up the market for alloy kit set boats. The labour, to build an aluminium kit set boat, is hugely reduced by the fact that that every part is already cut out. These parts then fit perfectly together like a jigsaw puzzle which takes away the highly skilled job of firstly lofting the boat and subsequently accurately cutting the parts to the lofted lines. If the cut files have been generated accurately, all the builder needs to do is match each part to the next and the boat should come out very fair and true. There is no excuse why any builder should not be able to produce a very professional product, assuming that the design of the boat is good and the cut files are accurate and of professional quality.
Typically kit set boats are conically developed. This means that the parts will lay on the surface of a cone (or usually multiple cones) and cylinders all joined together along a common radian or straight line. The key is that while the panel may look like it has curvature in both directions, at some point the surface must have a straight line representing the radians of the cone or cylinder. If this is done then the panels, can be “unrolled” onto a flat sheet. Some composite kits are developed for boats with compound curvature, but this can only be done with components that work together to make up the skins. For example a fibreglass cloth can be laid over pretty much any surface even if it has compound curves as can core materials that are made up of multiple small squares or cores that are planked up in thin strips like a cedar core.
However, then the skins have to be built up in parts adding resin and glues and building the skin up layer by layer which is very labour intensive and the cost of the materials can be quite expensive.
Flat Packs
This article is about conically developed panels more commonly plywood and aluminium. In days gone by plywood flat pack kits were popular but these days aluminium is more common. Aluminium offers both a material cost saving and also a labour cost saving. Plywood boats still make an excellent product. Very light and very stiff, but to make it durable it needs to be resinned, maybe glassed and painted. Resin, glass and paint add a considerable amount of financial cost and to do well takes many,many hours of hard laborious work. Aluminium can be purchased and cut in sheets as large as 9m x 2m. This reduces labour as there are very few joints required in the boat. Parts are merely cut from the right sized sheet. Aluminium can be left untreated. Weld it together, clean up the welds and you are ready to go boating. If you do want to paint, it is a far less arduous task than working from a fibreglass or wooden base.
Better Welders
In recent years, there have been great technological advances in welders. The machines on offer these days make welding very much easier and almost set themselves. This technology coupled with CAD design and CNC cut parts means that each and every part should be touching. We tell our kit set customers if it is not touching don’t weld it! It is hard to weld gaps in aluminium but if the cut files are accurate and the joints are tight, and you are using a good modern welder then the job is very much simpler and the finished product of much better quality.
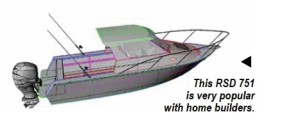
The availability of single-phase inverter welders for aluminium that are very cost effective has made building an aluminium boat feasible for home builders. These are high-quality welders that no longer require 3 phase power to run them. The builders can now build their boats in the garage at home with single phase power. No longer does it cost a fortune to buy a welder before you even start to build the boat and once you own one of these machines you will find it very useful indeed.1
Other tools required are mostly what any home handyman might have in his shed. A Jigsaw, a grinder, drills. It is a good idea to have a small single phase compressor and an air grinder and/or die grinder. These can be purchased cheaply from most hardware stores and once again are very handy to have even once the boat is finished.
Building Techniques
There are three ways to build an alloy kit set boat. The traditional way is to stand the frames upside down on a strong back or jig and build the boat inverted. One advantage of this method is the ability to “fair the lines”. It is easier to see the curves and check for fairness on a convex curve as opposed to a concave curve. The other advantage is that when you lay the sheets you have gravity working on your side and it may be easier to pull the panels down over the framework as opposed to pulling the bottom sheets into a female jig.
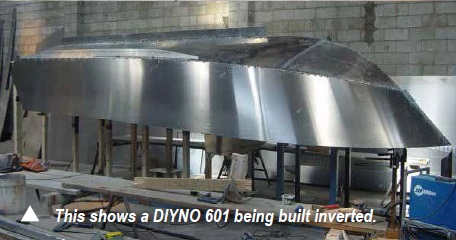
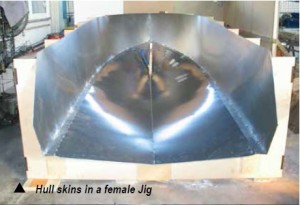
DIYNO Kitset Boats sell all their kits with a female building jig to build the boat the right way up. This is also CNC cut and slots together. The reason they use a female jig, according to Jim Pauling of DIYNO Kitset Boats, is it makes the set-up very easy. It takes skill to set up frames upside down the traditional way and if not done accurately then the hull panels will not fit at a later date. By using the female building jig, the hull skins are the first piece of the puzzle so you know that everything else has to fit if the skins have been pulled down into the jig correctly and aligned with the corresponding edges.
With the CNC cut parts, if the panels are accurately tacked together with the edges touching then the cut files themselves will ensure the boat is fair and true. The structure is all CNC cut as well so these effectively fair the hull skins by default when they are set in place.
Thereafter all the welding is down hand welding. This, says Jim, is much easier than welding overhead. For one thing, you don’t get showered in molten metal but also you have gravity working for you as you weld. Welding is making metal molten. If you are welding down into the panel, then gravity helps keep the molten metal where it should be.
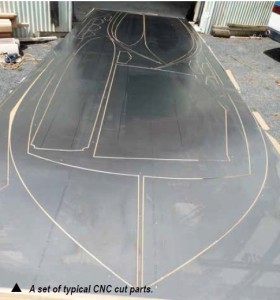
When you sit a welding ticket, you are certified for the welding position that you sat in the test. This is because it is harder to weld vertical and overhead than down hand. So building the boat the right way up in a female jig, he believes is the easiest way to get a good result particularly for non- professionals or first-time builders.
There is a third way of building the boat the right way up but without a jig, simply relying on the cut parts to hold the shapes. With this process, it is vital that all the parts may fit together, and that you don’t get any twisting as the build process proceeds. The small price of the jig ensures a very true finished product. As the boat is being welded, very high heat is put into the materials in the area of the weld. These materials expand and change the shape of the boat. You can imagine if you are welding on one side of the boat, the material there is hot and expanding while the other side of the boat is cool. Add to that the welds themselves are contracting as they cool. This puts stress on the boat that may not necessarily be balanced at any point in time. The weld schedule tries to spread the welds evenly around the boat to reduce the effect of this, but there are limitations. This distortion is counteracted to a large degree by the use of a jig. Without a jig, these stresses can in fact twist and distort the boat a lot. Even though all the parts of the hull may still fit, the twist may not be noticed until it is too late. With a female jig, once the skins are laid, all the structure is tacked in place before major welding commences holding everything in place as it tries to expand and contract. This also means that all parts fit together and there is no need to then individually modify and fit each part. This saves many hours of labour.
“We have done kits for professional boat builders who have always built boats inverted, starting with standing the frames. While I believe it requires more skill to do it this way it shows there is more than one way to skin a cat (or a monohull)”, says Jim.
Nelson based Ace Engineering are another player in the kit set alloy boat market and have a different approach. Jason Elvines owner of Ace Engineering, builders of the DNA range of boats and Pro-Kit kit set boats, says he got into the kit set market after initially been approached by an oversea’s customer already manufacturing boats, who wanted to enter the pontoon boat building market and also to change the look of their monohulls.
“Our customers have confidence in our designs and construction techniques because that’s our day to day business, so what you get from our kit sets is our refined techniques, step by step guidelines on building and welding processes from what we use on a daily basis”, says Jason.
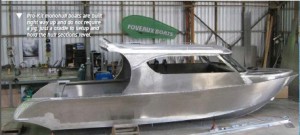
Pro-Kit kit set pontoon boats are built using a simple MDF jig cradle to hold the pontoon sections in place at the correct angle to form the ring and everything falls into place after this. The monohull builds are built right way up and do not require a jig, just a cradle to setup and hold the hull sections level.
“Due to the large hull panels being manoeuvred, from a fabrication point of view, room to move panels freely in or out speeds up fabrication time”, says Jason. This method is important to get things right from the beginning as it sets up the accuracy for the entire build. Jason adds that if his clients follow the instructions, building the boat is a very straightforward process.
“This process has proven popular in the Pacific Islands where it is cheaper to import the boat in parts and then assemble on site. In these cases, we usually pre fold all the panels ready for them to begin to manufacture immediately and even include windscreens”. Prokits hard top range comes standard with curved glass windscreens, which also provide a structural element to the hardtop design and cut down on the fabrication required in window pillars and roof structure as well as adding aesthetic appeal to the boat.
Why Build A Kit set Boat
So why do people build a kit set alloy boat? Some home builders simply have always had a desire to build their own boat and an alloy kit set gives them the opportunity to accomplish it in the least amount of time. Along the way, they develop some great new skills. Some builders decide to build an alloy kit set because they can get a better boat than what is on offer to them elsewhere and building it themselves allows them to customise the layout exactly to their requirements.
Home builders usually have to give consideration to the space they need to build the boat. Will it fit in the garage? Secondly how long will it take to build or how long will the wife’s car have to sit outside? Another great advantage of using alloy is it can be put outside without deteriorating.
If you have a solid week to put into the boat, you can work on it in the shed and then store it outside until you have another time period allocated to work on it again. It doesn’t even need to be covered when it is put outside. DIYNO offer an alloy jig to build the boat that then becomes the trailer. Once the trailer is built, the boat can be easily moved around.
It is unusual for production builders to offer much in the way of customisation. It is simply too expensive for a large production yards to do so. Guys building their own boats can customise elements of their boats. Designers of kit set boats need all the information they can from you, as a huge amount of design work goes into accounting for all the weights and the positions of weights of all the various parts. Changing these can have a big impact on the performance and handling of the boat so it is vital to work with the designer.
Christchurch based Robson Design has been in the business of producing kit set boats for a number of years for both the professional boat builders or a D.I.Y. enthusiast to build in their engineering workshop. The RSD models available as kits are all based on proven boats in operation throughout the world.
RSD systems have one of the largest range of alloy kits sets available in New Zealand with over 35 different models available in 4.5m to 16m, all designed by Robson Design. Robson Design was one of the first to produce full CNC cut alloy kits, supplying some of New Zealand’s top alloy production boat builders over the years.
RSD alloy kits are quite comprehensive and have been developed by the designers who have worked as boat builders so have been able to create very builder friendly concepts for the boats with emphasis to produce boats that do not require specialist boat building skills, just good engineering and sheet metal skills.
Robson Design can also custom design or modify an existing boat in its RSD range to suit client’s personal requirements or arrange construction for a partially built or completely turnkey vessel for any of the kits by one of the affiliated quality builders throughout the world.
Choose Carefully
So how do you achieve a successful outcome from building an alloy kit set boat? Choose your kit set carefully. Do your research on the design. It is a lot of money and hard work to achieve the desired outcome so choosing the right design from the start is vital. Look for a company that is happy to support you through the build process. It helps to have a good working relationship with the designer. As stated previously, one advantage of building your own boat is the ability to customise it. It is important to be able to discuss any proposed changes with the designer.
Give careful consideration to the materials used in the kit set. “We design our boats on the basis of 5083 alloys that has very good mechanical properties, but more importantly has excellent welded strength (up to 90% of the unwelded strength)”, says Jim. 5052 can be used, but the welded strength of 5052 is about 80% of the unwelded strength. The yield strengths are even less than these figures, 56% for 5052 and 77% for 5083.
While this does not mean that 5052 cannot be used, there may be some applications wheres 5052 is the right choice, but the welded strength of the alloy needs to be taken into consideration. The cost of 5052 is considerably cheaper than 5083 and therefore tempting to substitute for 5083. However, 5052 should never be substituted for 5083 if the boat has been designed and engineered for 5083. We have had potential suppliers tell us in the past that 5052 is just the same as 5083, just not marine certified. This is wrong and potentially dangerous! Check that the material supplied in the kit is the material specified in the design and sourced from a reputable supplier.