Pacific PowerBoat Magazine is excited to continue our series on the build process of the Bill Upfold-designed Elite 22M Flybridge Motor Yacht. Currently under construction at Weber Marine in Gulf Harbour, Auckland, this journey takes us from initial concept discussions with the owner to its on-water launch and culminates in a detailed review scheduled for late 2026.
This 22-metre masterpiece combines cutting-edge engineering with bespoke luxury. Constructed using epoxy resin, E-glass, and a PVC foam core over a male mould, the yacht promises to be both weight conservative and robust.
The design includes four staterooms:
A full-beam master suite amidships.
A VIP stateroom forward.
Two twin guest cabins, all featuring ensuite bathrooms.
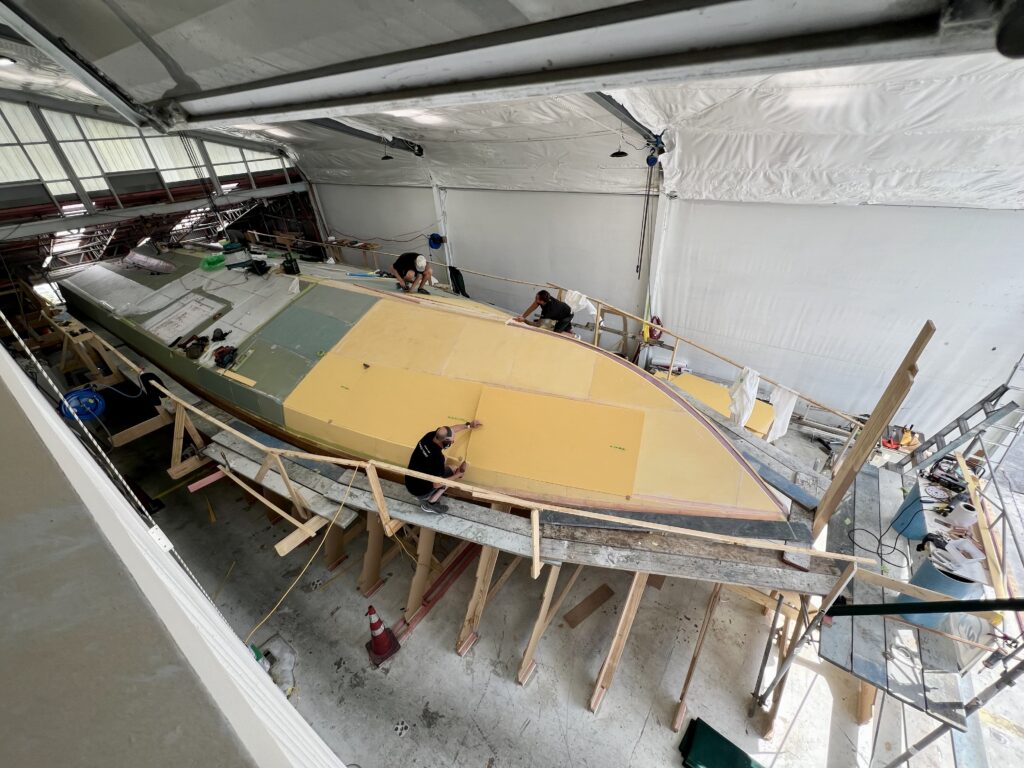
Part Two
Hull Construction Underway
As illustrated, the hull construction is progressing well, using a modern composite foam core build method, which departs from traditional practices.
Full Composite Foam Core Build Method
For this large, fast 22-metre yacht, the team has opted for a full composite foam core for the hull construction, utilising epoxy resins for its superior strength-to- weight ratio over polyester resin commonly used for production yachts.
1. Sacrificial Mould: The male frame is covered with 12mm MDF and wrapped with PTFE release tape, allowing the hull to detach cleanly.
2. Fibreglass Layers: Multiple layers of fibreglass form the inside skin of the hull.
3. Foam Core: The core is vacuumed to the inside skin, ensuring even resin distribution and avoiding air entrapment.
4. Reinforcement: High-stress areas, such as rudders, shafts, stabilisers
and skin fittings, are reinforced with multiple additional layers of fibreglass.
5. Outer Layer: The exterior fibreglass laminate is applied before the addition of lifting strakes, filling, fairing, and painting.

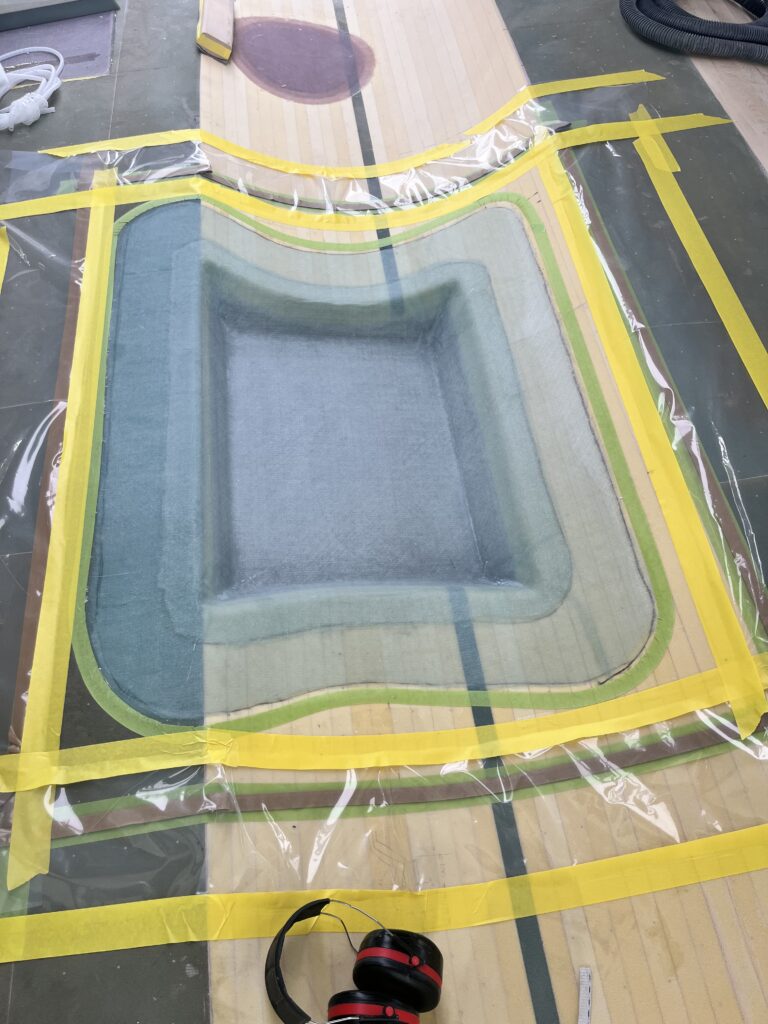
Benefits of the Upside-Down Build Process
As the build progresses, the intention is to have the hull upside down as long as possible, enabling the internal structure to be installed, including all bulkheads, integral tanks and partitions. Key advantages of this approach include:
1. Dust and debris falls to the ground beneath the hull when working inside. (easy clean up).
2. Internal teams work on a level surface rather than the angle of the hull.
3. Tasks are performed at a comfortable height, reducing strain.
4. Simultaneous internal and external work accelerates the timeline. The fairing team is on the outside, and the building team is on the inside.
5. Bilge painting in a dust-free environment.
6. Bulkheads and all other structures being already in place ensure a stiff and braced structure for when the hull is turned.
Stay tuned as we continue to follow this innovative build and provide updates on the progress of this exceptional vessel.