Sam Power, Technical Sales for Henley Engineering, looks at what the options are if you damage your propeller and offers some advice on propeller care.
Propellers are a vital component of the marine driveline and the key ingredient when converting an engines output torque into forward thrust. The importance of correct sizing and blade condition should not be underestimated for driveline efficiency and engine health.
When looking at a propeller there are three basic aspects relating to prop performance; diameter, pitch and number of blades – these are usually expressed in the following format of imperial measurements; 11” X 15” 3B. This example would describe a propeller of 3 blades with 11” outside diameter and a theoretical pitch of 15”, meaning; if placed into a solid (block of jelly for example) and turned one full rotation – it would move forward 15”. This does not happen in the real-world application because of slip factor when operating in a liquid and trying to push a heavy hull, hence, “theoretical” pitch.
Propeller sizing, manufacture and repair have come a long way in the past 20 years, to the point that there is almost no “guess work” involved. Companies such as Henley Engineering now work with long proven mathematical calculations, Prop CAD software, decades of sea trial data and the latest MRI propeller scanning equipment – which provides detailed reports before and after the adjustments or repairs have been made.
This isn’t to say that the sizing strike rate is 100%, considering all the factors involved in a propeller calc and the importance of accurate input data. However, by utilising this knowledge and technology you greatly increase your chances of maximising performance and efficiency while avoiding additional haul outs, blade adjustments and fuel costs. These are the potentially very costly hidden dangers of incorrect propeller sizing/ repair that can often sting boat owners who have been lured in with a hugely discounted price. The well-known proverb “the poor man pays twice” often applies in propeller world (sometimes thrice!).

WATCH OUT FOR THE BUMPS
With modern day GPS we are fortunate to be able to safely navigate the coastline, however, run-ins with a reef, rope, ramp or logs can and do occur. So, what to do when the unexpected happens and you’re left with a nasty vibration?
Firstly, do not attempt to straighten the propeller yourself; it may look better, but it is very unlikely the blade will be within the required tolerances. More importantly, when using incorrect equipment and techniques you run the risk of cracking a blade and or further damaging other driveline components. Significant bends are carefully straightened with heat applied within a strict temperate range.
The propeller should be removed and sent in for repair assessment. In our workshop this process can include; clean off, MRI Prop Scan, visual assessment and NDT dye penetrant crack testing. In cases of serious impact damage, the shaft and half coupling should also be properly assessed for damage as even the slightest bent shaft or coupling register runout can cause vibration and subsequently, damage to other driveline components.
REPAIR OR REPLACE
In our current throw-away society, many boat owners are quite receptive when presented with the option of propeller replacement, when, in most cases (especially for bronze propellers) this should be a very last resort and often is not necessary. Propellers are an expensive part of your vessel that should have been custom designed and manufactured to suit. If looked after properly and protected from galvanic corrosion, they can, in some pleasure craft applications, be in use for over half a century! This is evident in commercial applications where a propeller may have more than 10 significant repairs over many thousands of running hours that the casual or even serious all year round boatie could never hope to come close to logging.
We are often asked about the availability of second-hand propeller options – the reality is there are not many and it often means compromise or a long financial cluster! You will need to match; blade area, blade number, rotation, pitch, diameter, hub diameter, bore diameter, keyway, taper length and angle. These are all carefully considered when designing a custom-built propeller. You have a better chance with outboard or sterndrives but still the options are few and far between.
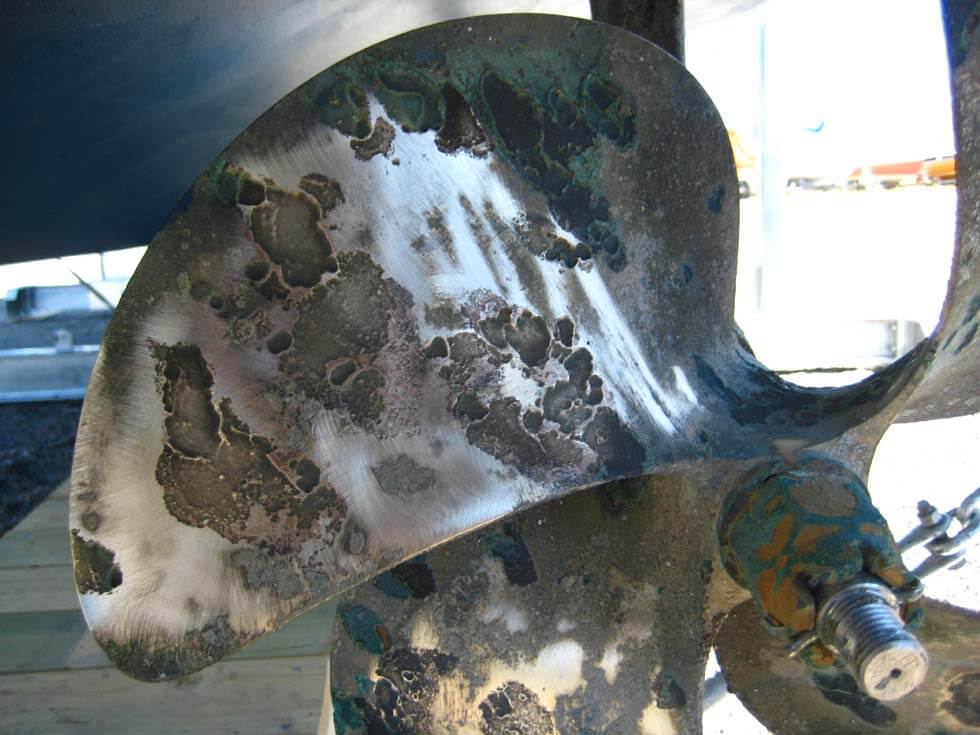
When dealing with experienced prop technicians the repairability of bronze, aluminium and SS propellers is very high and people are often surprised at what can be repaired to an as new condition (both in terms of performance and appearance). However, it is important to beware of “marine panel beaters” who lack the necessary precision equipment and knowledge to complete the repair to the required international ISO standards and provide “proof” of before and after results. Beware of “Snake oil” answers.
These standards refer to blade pitch, cross section tolerance (measured with MRI Prop Scan technology) and surface finish. Blade balance is also an important factor but accounts for significantly less of the experienced vibration than blade pitch tolerance. You should ALWAYS request a copy of the before and after Prop Scan reports as this provides proof that the repair was carried out to the correct tolerances and gives an accurate record of the pitch measurement (which can vary up to 2” from the stamped size depending on the manufacturer).
PROP RELIABILITY
The main factors affecting a propellers repairability are; galvanic corrosion/ electrolysis, volume of blade material and of course the extent of the damage to begin with.
Galvanic corrosion occurs when dissimilar metals are placed in salt water, with the least noble becoming the sacrificial anode and more noble the protected cathode. It is the silent killer in the propeller world and can cause thousands of dollars in damage in a matter of weeks. A common cause of propeller corrosion is failing shaft bonding straps. The carbon brush type, if not properly cleaned and maintained can develop a film, which breaks the circuit and isolates the driveline from the zinc.
So, what’s the big deal? – Bronze affected by galvanic corrosion becomes very brittle and prone to cracking, it is also difficult to weld to as the corroded parent material now differs in composition from the original material specification. Because insurance policies do not cover galvanic corrosion, even the slightest bent blade from impact can render the propeller a write off at the expense of the owner. Understandably this news is not often well received.
COMBATING GALVANIC CORROSION
How do we combat galvanic corrosion? Shaft and transom mounted anodes are the best solution as they can be easily checked, replaced and it is obvious to see if they are working. Threaded bullet anodes mounted aft of the propeller are preferred to the clamp style as they do not disrupt waterflow to the propeller. If shaft straps must be used, then ensure they are always bonded correctly and carefully maintained as per the manufacturer’s instructions. Your propeller should be regularly checked for any pitting or discolouration.
Propellers are manufactured in 3 different blade materials; bronze (generally larger moored vessels), stainless and aluminium (smaller trailer boats).
Bronze propellers are primarily custom made to order in either NAB (nickel aluminium bronze) or MAG (manganese bronze). Most older propellers are MAG with the preferred and superior casting material today being NAB for its higher tensile strength and corrosion resistant properties. A bronze propeller in as new condition can be re pitched up to 3”. Cracks, bends and even missing blade tips can be repaired depending on blade thickness and material condition.
Stainless propellers are mostly reserved for outboards and sterndrives for which they are mass produced. So, the availability of sizes off the shelf is very good. Stainless steel is more difficult to repair than bronze but the high cost of replacement makes it worthwhile in most cases, especially for duo props. The blades are more difficult to adjust and usually 2” re pitch is maximum. They are also more prone to cracking and sub-par crack repairs are common. Welding over the crack and grinding back is not good enough as it results in a very thin and weak repair. Because of the higher operating speeds, it is especially important that the blades are repaired to within the correct ISO tolerances to ensure smooth running and prevent gearbox damage.
Aluminium propellers are only suited to lower horsepower outboard and sterndrive applications because of the softer material. They are not suitable for higher speed applications and the blades must be thicker than stainless steel. These are the cheapest option available (approx. ½ the cost of stainless steel) so are often not worth repairing unless they are duo props. If looking at repair it is worth checking the rubber hub insert as if this is damaged or has spun then complete propeller replacement is the best option.
THE RIGHT FIT
Propeller fitment is the final piece of the propeller repair puzzle. For outboard propellers; ensure the spline is clean then reapply an even coat of marine grease. Slide the thrust washer over the spline, then slide the propeller over the spline, washer, nut and finally either folding tab washer or split pin depending on the requirement. Always carefully check the tab washer or split pin if you are planning on reusing the old one as failure can result in a lost propeller!
With larger bronze propellers running on a shaft taper it is important to check the fit before installation. All new Henley propellers are lapped, ideally to the drive shaft or if not available then to a matching mandrel to obtain a 100% blued contact fit. This is a very important part of the build process, as it is the friction of the two tapers that locks the shaft and propeller together – not the key, which is just a backup. Some propellers and shafts run without keys.
Because of this it is very important to never grease or apply anti-seize to any driveline tapers, if a propeller or half coupling is difficult to remove it is usually a good sign indicating good taper contact. When tightening the prop nut care must be taken not to bend the blade tips, to lock the propeller in position use a wooden block either to the hull or ground which is seated as close to the blade root as possible – not at the tip. Finally, and most importantly – check your anodes!