The Vetus Marine Combiflex coupling has been designed to ensure optimal damping of torsional vibration.
While you may understand the basic working functions of the marine diesel in your boat, have you ever taken the time to appreciate how all that power gets into the water, so the thrust and performance are smoothly and somewhat vibration-free as it is transferred to the propellers. A lot of focus goes into reducing and containing noise and vibration within a vessel’s engine room so those same fundamentals should be applied to what’s around the engine. Reducing vibration comes in a variety of ways, with the most common being engine mounts and flexible driveshaft couplings.
It is not often there’ll be an abundance of space left within a hull or engine/propulsion area to configure a bulky driveshaft. Any extra length or height required in your layout will encroach on available cabin or service area space. Engines are often positioned to balance out the weight of other plant and equipment so in some instances a longer series shaft may be needed with support bearings fitted at the midpoint.
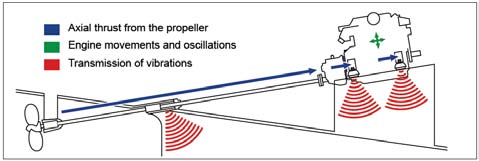
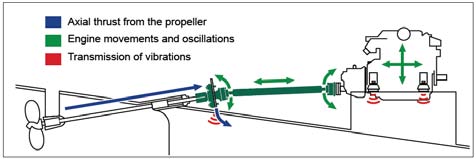
Dealing with Thrust
By combining thrust bearings with a marine Cardan or CV shaft, you get the perfect solution for conventional shaft drive vessels, reducing noise and vibration and simplifying engine installation and shaft alignment. Thrust vibration is absorbed through rubber pads mounted parallel to the propeller shaft. Rubber performs better under compression, by incorporating these units to absorb all the thrust in the design, softer engine mount material can be used further enhancing the reduction of noise and vibration. Without the absorption of thrust at the propeller end of the drive line, you risk the transfer of thrust and shock to the gearbox that can be costly to repair if damage occurs.
The ability of universal joints and CV joints to operate at a considerably higher angle than other coupling designs compensates for hull and mount movement over time reducing vibration and load on the propeller shaft seal. Without an independent thrust bearing, thrust is transferred through the gearbox to the engine mounts.
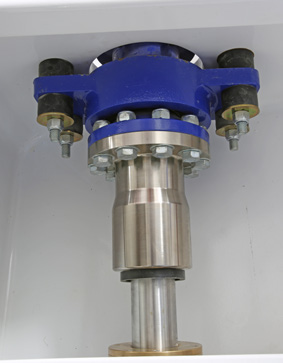
There are various flexible coupling solutions that sit between the Shaft and the gearbox that offer a tortional damping function though it does not manage misalignment like the flexible shaft options. Such a flexible coupling combined with a correctly selected mounting system dampens the torsional vibration coming from the engine and gearbox to the hull.
Vibration Solutions
Turret Driveline, a product of Australasian based, Beattys Driveline Technologies, offer a range of driveline solutions, comprising of driveshafts and cv shafts along with their own Turret thrust bearings, to ensure power is transferred quietly with minimal vibration. The drive train is isolated from the engine with thrust bearings and universal joints to take the load off the engine mounts and transmit the thrust directly to the hull. Beattys motto is that driveshafts should be seen and not heard!
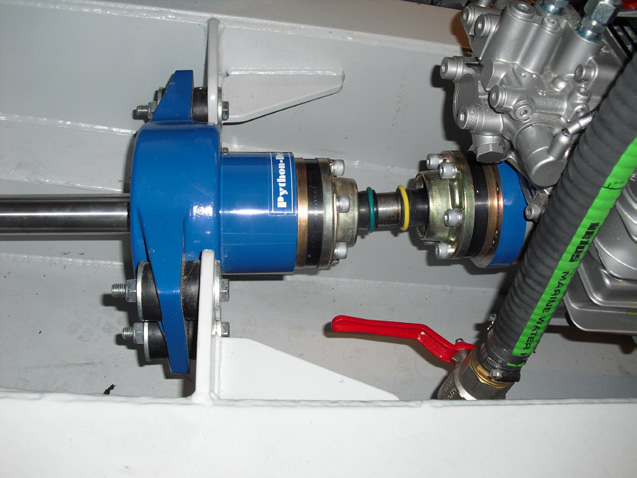
Python-Drive is another option, which allows the propulsion system to push your boat, not your engine. This separates the propeller noise and vibrations from the engine while eliminating the need for perfect shaft alignment. Python-Drive Systems are available for engines from 10hp to over 1000 hp. Maintaining perfect alignment of the gearbox to the propeller shaft is no longer necessary with the use of a Python Drive. Even with unequal angles the Constant-Velocity drive shaft guarantees a constant speed of the propeller shaft and reduces wear of other parts of the drive line. An internal taper clamp shaft connection makes fitting the shaft to the thrust bearing a simple task, plus the thrust bearings and CV shafts can be used as standalone units to fit your application.
Sigma Drive is manufactured by Bruintons Propeller in the UK, renouned for propulsion excellence, is yet another thrust bearing and CV drive shaft system available for applications up to 1300hp. The sigma drive CV can also be used independently as a thrust coupling but combined in pairs with the Sigma thrust bearing offers the ultimate in vibration and noise reduction.
Aquadrive, manufactured in Sweden is one of the world›s most recognised manufacturers of anti-vibration systems, offering engine mounts, CV shaft and thrust bearing systems. The CV shaft of variable length includes two true plunging Constant Velocity joints that work independently at any angle. This eliminates the need for accurate engine alignment, either during initial installation or subsequent use. The rolling action of the balls within the CV joints absorb all axial and radial loads, permitting the use of very soft engine mounts as well as reducing wear in connected bearings. A range of pre- machined adapter kits allows coupling to almost any marine gearbox.
Craftsman Vector Drive is available for shaft torques up to 1100 Nm and thrust forces up to 11.5 kn. It features a Constant velocity (CV) shaft available in different lengths, permissible angles up to 8° per side of the CV shaft. It has an easily accessible clamping hub, which is self centring and self adjusting.
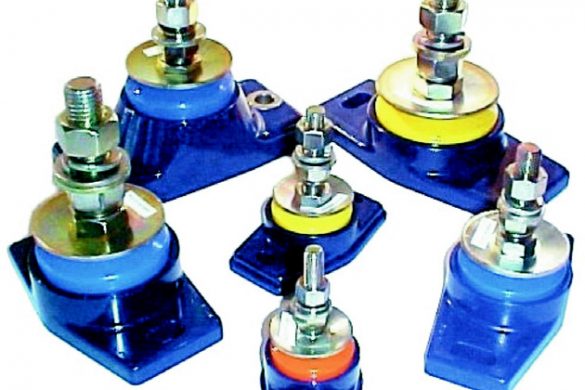
Vetus Drive has a combination of a self-aligning thrust bearing and a double acting constant velocity joint. The propeller thrust is absorbed by the inbuilt thrust bearing allowing the engine to be set up on softer mountings, resulting in lower vibration and transmitted noise. The VDR is made of stainless, black passivated steel and high performance rubber and is suitable for maximum thrust up to 24 000 N.
Poseidon Orion flexible couplings are developed to operate with or without propeller thrust and can be installed as a single or twin type. The Heracles thrust blocks are Poseidon’s latest innovation and come complete with flexible mounts. The Orion thrust blocks are equipped with a twin spherical bearing set and offer a regular and a short building version. The Orion thrust blocks can be installed either rigid or flexible.
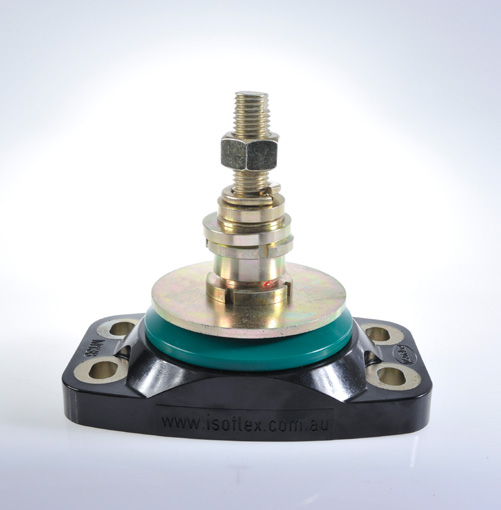
Flexible Couplings
Poly Flex flexible disc transmission couplings provide a damper between the gearbox and propeller shaft to isolate torsional vibration from the engine and gearbox. It also reduces the shock of forward and reverse gear changes. The couplings work in conjunction with the engine mounts by providing the softest element in the shaft assembly to improve performance. All metal components are plated in SA5 Cobalt Zinc for maximum corrosion resistance and durability.
The moulded components are manufactured from Polénite a special range of engineering heat-cured polymer alloys. Unlike most mounts, the polymer is not bonded to the steel, so worn Poly Flex mounting systems can be rebuilt rather than scrapped and replaced individual components can be renewed. All the parts are designed, engineered and manufactured by Poly Flex in Brisbane.
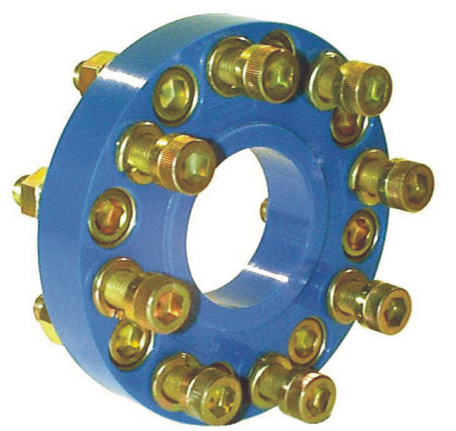
Isoflex, also made in Australia also offer a gearbox coupling similar to the Poly Flex unit. Designed as a “sacrificial link”, to fail before gearbox damage occurs, they are intended to cover a large percentage of Twin Disc and ZF gearboxes, plus many other boxes found on the market.
R&D Marine offers a wide range of flexible shaft couplings that consist of a contoured flexible disc moulded in resilient polyurethane. The contoured disc gives clearance for the bolt heads. It can flex freely to take up any temporary misalignment of the engine and shaft, due to flexing of the boat structure or the engine moving on its rubber vibration isolation mountings. In the unlikely event of a disc failure, the steel straps make the coupling fail safe and ensure the drive is maintained in both forward and reverse.
Vetus Marine Combiflex coupling has been designed to ensure optimal damping of torsional vibrations, created by cycle irregularities, especially at low revs. The flexible rubber element ensures low-noise and vibration-free transmission, without backlash between the engine and the propeller shaft. The Combiflex coupling is secured against shearing off, both axially and radially, thus ensuring safe transmission under all circumstances.
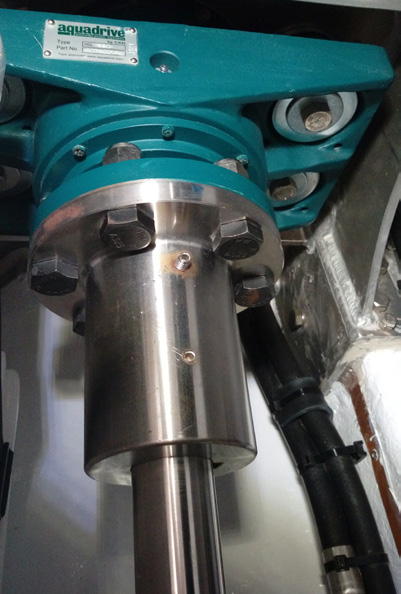
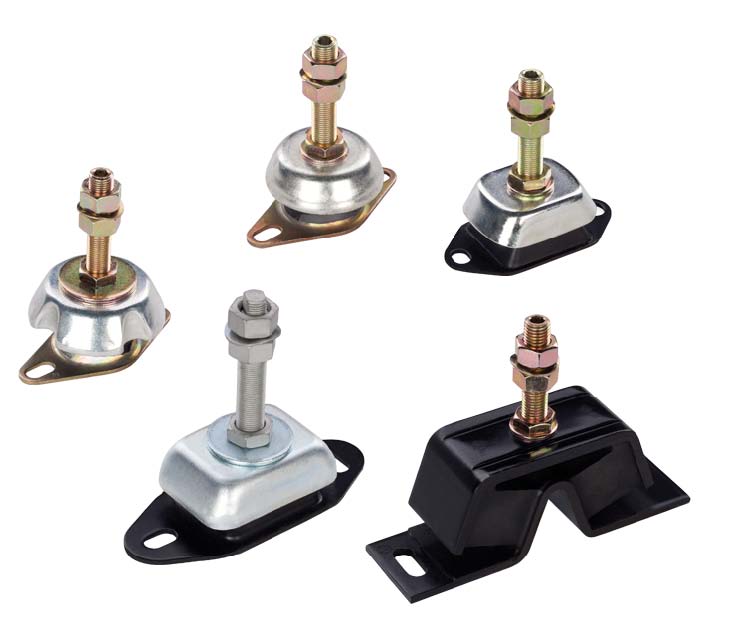
Resilient Mounts
Let’s move forward to the engine end of things again. Resilient mountings are necessary to reduce transmission vibration. Engine mounts play a crucial role in preventing engine vibration from passing to the boat. Just about every engine already comes with the factory approved mounts, but they’re several ‘after-market’ brands available which are explicitly designed to reduce engine vibration.
If your engine mounts are more than five or six years old or have been contaminated with seawater, engine oil or coolant, change them. Even if the mounts look perfect, the tough elastomer (rubber-like) material in the engine mount work -hardens over time and ceases to isolate the boat from the engine’s vibrations. Seawater rusts the metal parts of the mount and can cause delamination of the elastomer and metal parts. Rust also weakens the mounting bolts and in extreme cases can cause bolt failure. Engine oil and coolant deteriorates the elastomer and also hastens delamination. Poorly aligned engine mounts can also cause bolt failure. And, if you have noticed screws backing out on your boat, or if your oil pressure sensor has failed recently, then the root cause may be increased vibration due to bad engine mounts or a misaligned shaft.
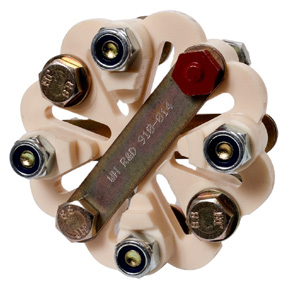
It is also important that the engine mounts be properly loaded so they are equally carrying the engines weight. If one mount is not carrying the same load as its mate then there will be inherent vibration problems. There are several brands of engine mounts on the market, and while they all mainly do the same job, there are differences between brands.
Poly Flex mounting systems are designed as true marine propulsion engine mounts with sufficient vertical deflection to obtain proven vibration isolation. They have controlled
minimum thrust and lateral deflection under propulsion load and inertia due to sea conditions. They are designed to have a fail safe that in the event of a capsize the engine will not break away from it’s bearers.
They have over 200 models suitable from 10 to 2500hp and are continually expanding their range. All their couplings as well as mounts are available with DNV Type Approval and are moulded from heat cured polymer alloys, which are both oil and fuel resistant.
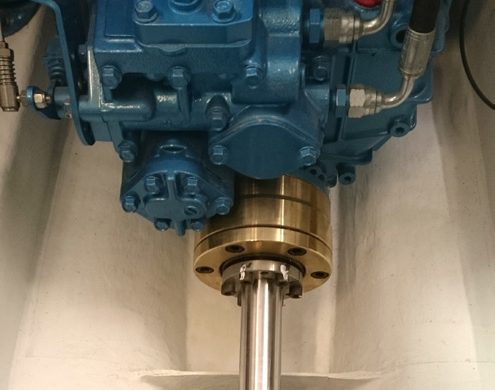
Isoflex mounts are designed specifically for marine applications and contain no rubber components, which suffer from degradation due to oils, fuels and water. Isoflex›s engineering polymer materials make for long-lasting use and durability. They are available as a fixed bolt down or adjustable mounting system, the latter being ideal for retrofitting. Aquadrive’s proven engine mounts are softer than almost any other and come with a steel hooded to prevent diesel damage and are fully captive so that the engine cannot leave its frame even if the vessel is turned over.
R&D Marine’s engine mounts feature a fail-safe system, slotted holes in the casting to assist alignment, height adjusting to simplify alignment and all parts are zinc plated & passivated.
Vetus Marine has a range of flexible mounts that contain a special rubber compound with excellent vibration damping properties.
They range from the K40 which has a loading of 40kg, through to the LMX500 suitable for marine diesel engines in the power range between 70 and 350 kW (95 – 480 HP). It has a maximum load of 500 kg.
Craftsman Marine offer a range of flexible mounts with 45kg to 150kg load capacity. The CM type 9 and 10 are extra flexible to absorb more vibrations in light boats that would otherwise be transferred to the hull.
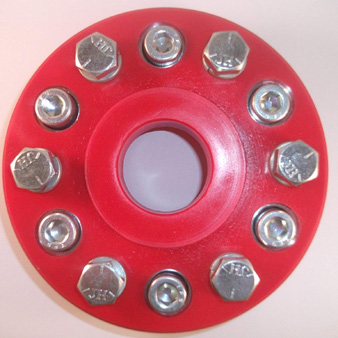
Strut & Shaft Science
The placement of the strut itself can have a significant bearing on things too. If it is located further away from the stern tube bearing in front of it than a distance equal to 4 times the diameter of the shaft, that shaft is likely to begin to behave like a skipping rope being swung between two vigorous girls. Similarly, allow more than one shaft diameter between the rear of your strut bearing and the front of your propeller boss and the prop becomes prone to wobble about like a limp wrist.
This may all seem like a bit of a juggling act, but, if you don’t get this end of the business right to start with, no matter how light your hull, how fair it’s bottom, or how hairy-legged the horsepower you will be disappointed with its performance. The actual size of the prop shaft will depend on how much horsepower it is being asked to transmit and at what revs, and the prop man is the best guy to establish this, as there are materials of different tensile strengths to take into account. However, firstly you need to make sure you have your engine set upright, and by using flexible drive shaft couplings and suitable engine mounts, will go a long way to making sure what goes down the drive shaft is just power.