From Installation to Use
Article by boattest.com
“Trim the dish!” was an order bellowed by the coxswain of a ship’s tender in the age of sail, a command indicating bodies needed shifting in order to restore the craft to proper trim. Fortunately, today’s captain isn’t limited to delicately asking big-boned Aunt June to reposition her considerable bulk in efforts to provide a smoother ride. Trim tabs provide an easy, touch of a button solution for making those on the fly adjustments. Here’s the low down on trim tabs — what they are, how they work and how to select the right type for a given application.
A COMFORTABLE RIDE
A properly trimmed boat is not only safer to operate, it also provides a more comfortable ride, as well as better speed and increased fuel economy. While trim tabs let a captain adjust a boat’s trim when moving, it’s best to achieve static (non-moving) trim to the extent possible before getting underway. This can be as simple as balancing a boat by distributing weight (passengers, coolers, portable fuel tanks, etc.) to keep the hull floating level.
Achieving stationary trim is one thing, however we’ll need to make adjustments once underway to account for speed, water conditions and direction of travel (with regards to waves and wind). Smaller boats, for example, will ride bumpier in surface chop if left trimmed at calm water angles. With an outboard or stern drive, an operator can control bow attitude its tilt and trim feature, but it’s trim tabs that let a captain make side-to-side adjustments
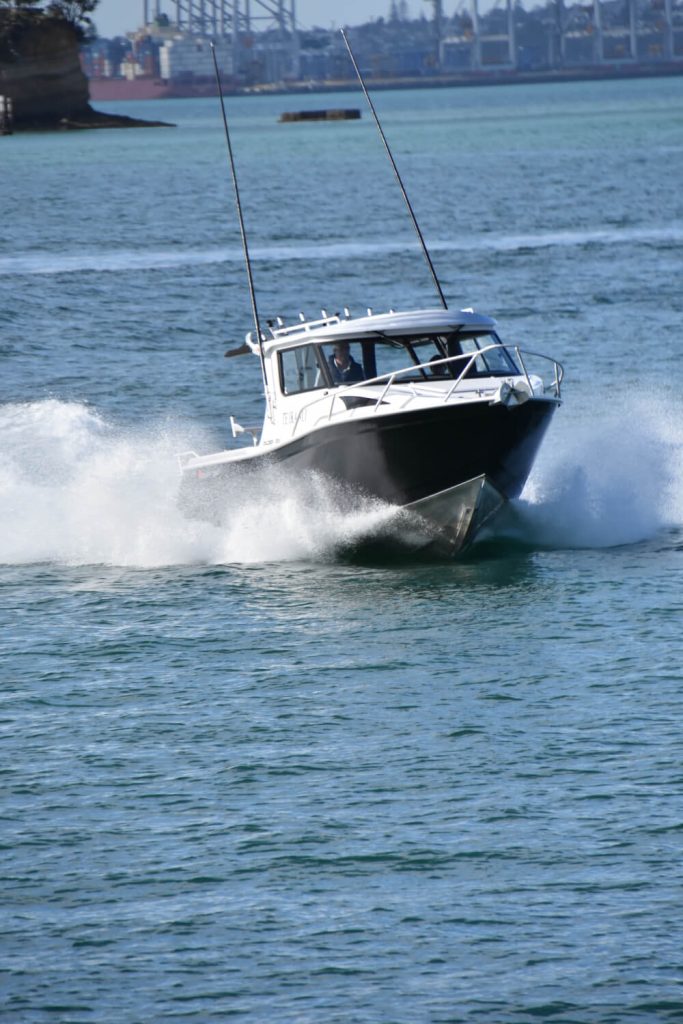

The Right Type
Adjustable trim tabs come in two types: hydraulic and electromechanical. Which style is best is typically a matter of personal opinion, however there are pros and cons associated with each.
Hydraulic trim tab planes are controlled by hydraulic cylinders that are actuated by a hydraulic pump. The pump, motor and associated equipment for the entire system is installed inside the boat in a dry, more-protected environment. On the downside, because they require the installation of a hydraulic pump and hoses, hydraulic trim tabs are a bit more complicated to install than electromechanical systems — although not overwhelmingly so.
Electromechanical trim tabs utilize electric actuators to move trim tab planes up and down. Because the actuators immediately stop and start when the control switch is pressed or released, they can provide instant response times and precise control.
In an electric trim tab system, everything (electric motor and gear system) is located on the outside of the transom. This simplifies the installation somewhat, but it also runs the risks associated with having electronic components underwater.

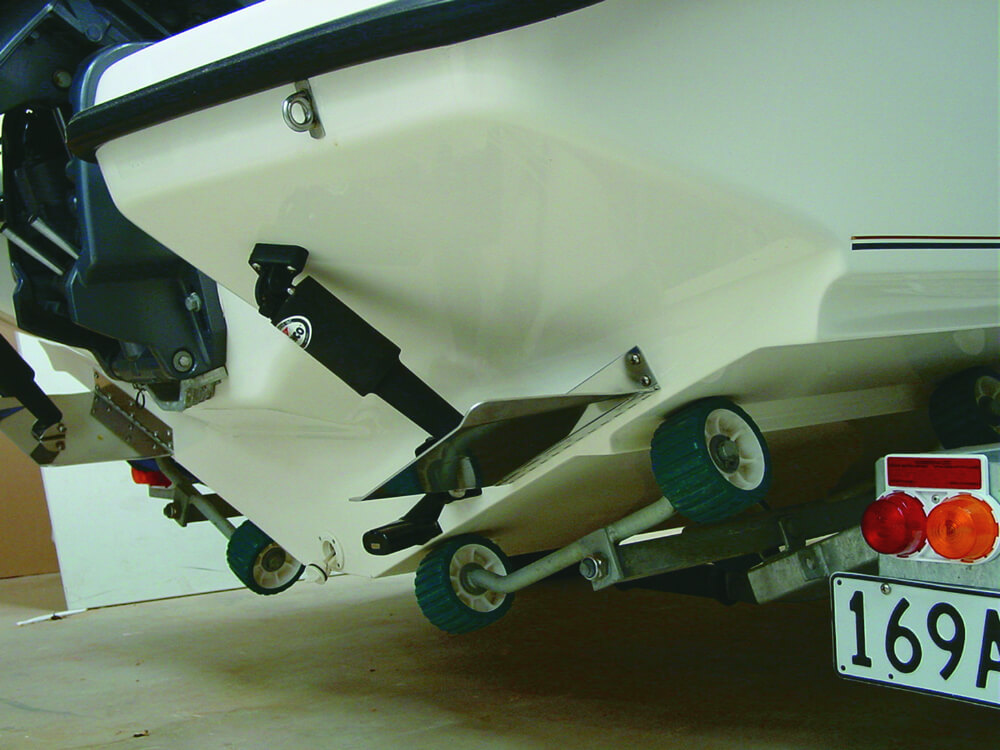
Both systems utilize an electronic control switch or joystick located at the helm. Pressing the switch or toggling the joystick generates an electrical pulse. This energizes the hydraulic pump or electric motor for the trim tab planes (depending on which system is installed).
The trim tab planes themselves come in a variety of sizes. Trim tabs for high-speed boats tend to be long and narrow, while smaller, slower boats will generally use wider, shorter planes. The best way to select the proper size for a boat is to consult with the trim tab manufacturer.
Installation
While having trim tabs installed by a dealer or boat yard is a common option, the installation is well within the ability of any competent DIYer. As with any installation, the trick is to read the installation instructions and understand them completely prior to picking up that drill. A typical installation should take around five hours, depending on the boat.

Rules to Trim By
While everyone should follow the instructions provided by the trim tab manufacturer, the following general tips can be applied to most any installation.
When determining the location of the trim tab planes, keep in mind that the farther out the tabs are from the hull centerline, the more effectively they will operate. Also, make sure both tabs are symmetrical — i.e. mirror images on each side.
While determining the location of the trim tabs and actuators, verify there are no obstructions inside or outside of the transom that will interfere with the installation. This includes double-checking that an installer will not be drilling into hoses, equipment or wire runs.
If the boat has an outboard or stern drive, verify that the trim tab locations are located outside of their steering angles.
When drilling, run the drill in reverse until through the gelcoat (to help prevent chipping) then switch to forward and continue drilling. Beveling each hole will help prevent future gelcoat cracking and provides a better seal once caulking is applied.
If the transom is solid fiberglass, drill the holes for the mounting hardware and use a good quality, marine-grade sealant during the final installation. For a cored transom, seal the exposed coring with epoxy resin to prevent water intrusion into the core. Alternatively, one can also drill the mounting holes slightly larger than needed, fill them with thickened epoxy, then drill the properly sized hole through the epoxy plug when cured.
Once all holes are drilled, dry-fit everything to ensure a perfect fit prior to bedding (caulking) and final installation.
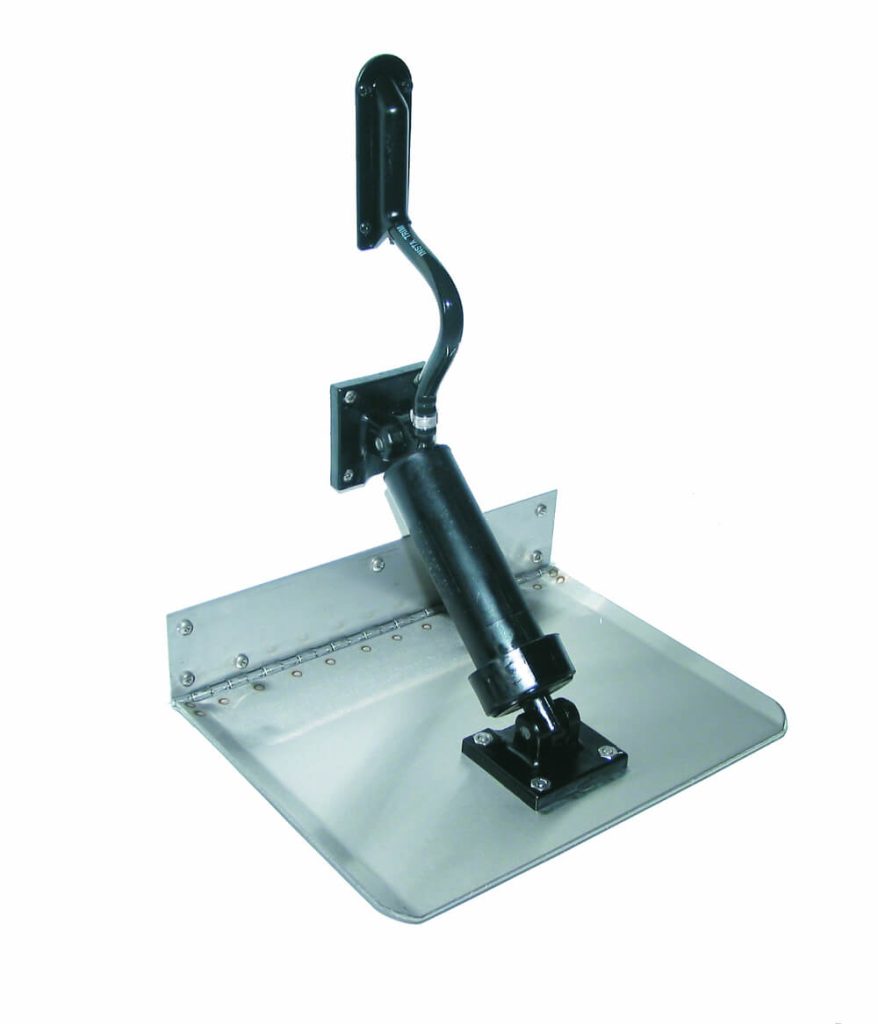
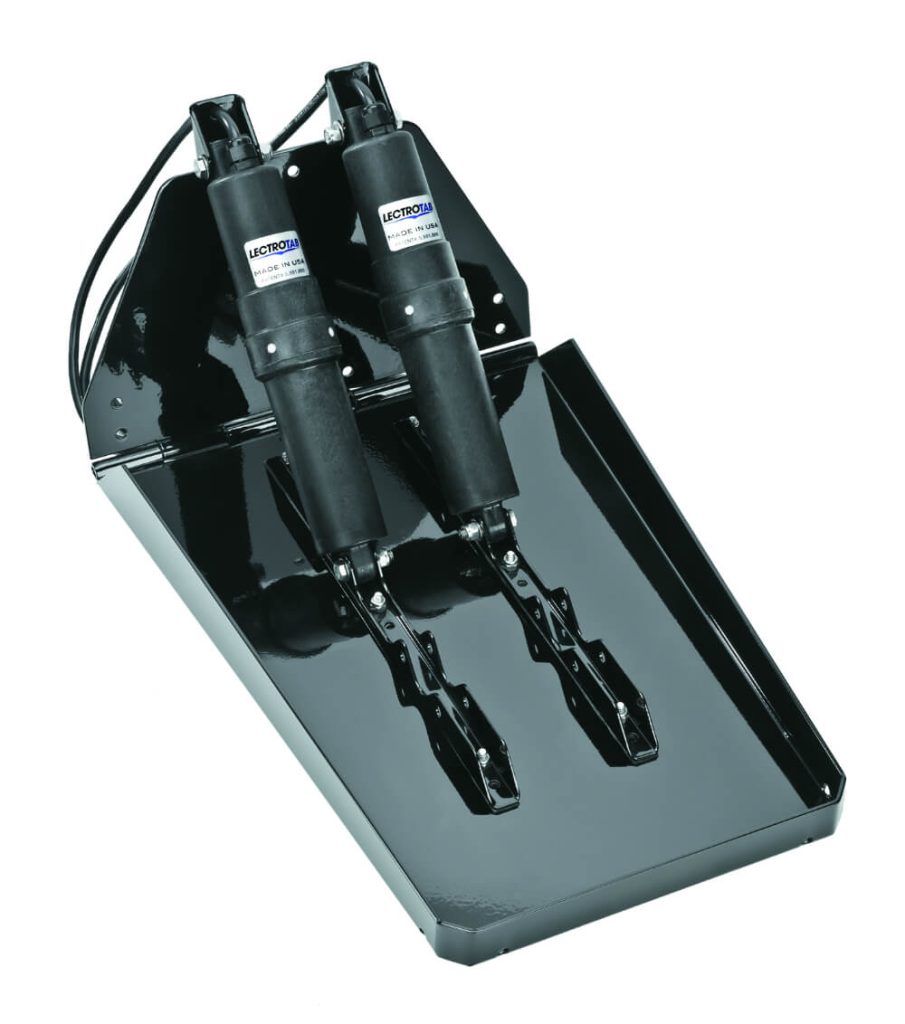
INTERCEPTORS – ANOTHER ALTERNATIVE
Interceptors are a very unique answer to the question of boat trim and while until recently were the domain of bigger boats (over 12m) they are now readily available and specifically designed for trailer boats. There are three brands of interceptors available in Australasia, and they all come from Sweden. Humphree, (also marketed through Volvo Penta as Interceptor), the first to commercially promote interceptor technology, Zipwake, who offer a broad range of units especially suitable for both cruisers and trailer boats and Volvo Penta with their Boat Trim System (BTS).
The interceptor blade is to create pressure underneath the hull, at the stern of the boat. The pressure is created when the blade is deployed into the water flow underneath the hull. Despite what you first might think there is only a minor deployment needed to create a large lift force under the hull. This lift will change the running trim of the vessel resulting in a lower wave resistance. The interceptor’s main function is to create a lift force in order to reduce the hull’s wave resistance. The same function is generated by a traditional trim tab. With reduced wave resistance, the interceptor generates more lift force and less drag than trim tabs. The key to achieve good results is the speed of control. Traditional trim tabs are generally very slow as a result of the amount of water they need to push when deflecting the tab.
As such, the automatic functionality will suffer severely not being able to handle the motions in a safe and comfortable manner. Since the interceptor blade does not push away the water, it can move easy, allowing them to move much faster than trim tabs. All interceptor systems electric powered by 12-24 Volt DC. Thanks to the design of the Interceptor it only requires a small amount of power to move the blade up and down, even under high-speed operation. The Interceptor blade is controlled by an electronic actuator, which is designed too move the blade a full stroke as fast as 1 sec, which is considerably faster than conventional trim tabs. By their design they are lighter than most trim tabs can also integrate easier to the transom and in some cases can be custom shaped with a curve to follow the shape of the hull bottom.
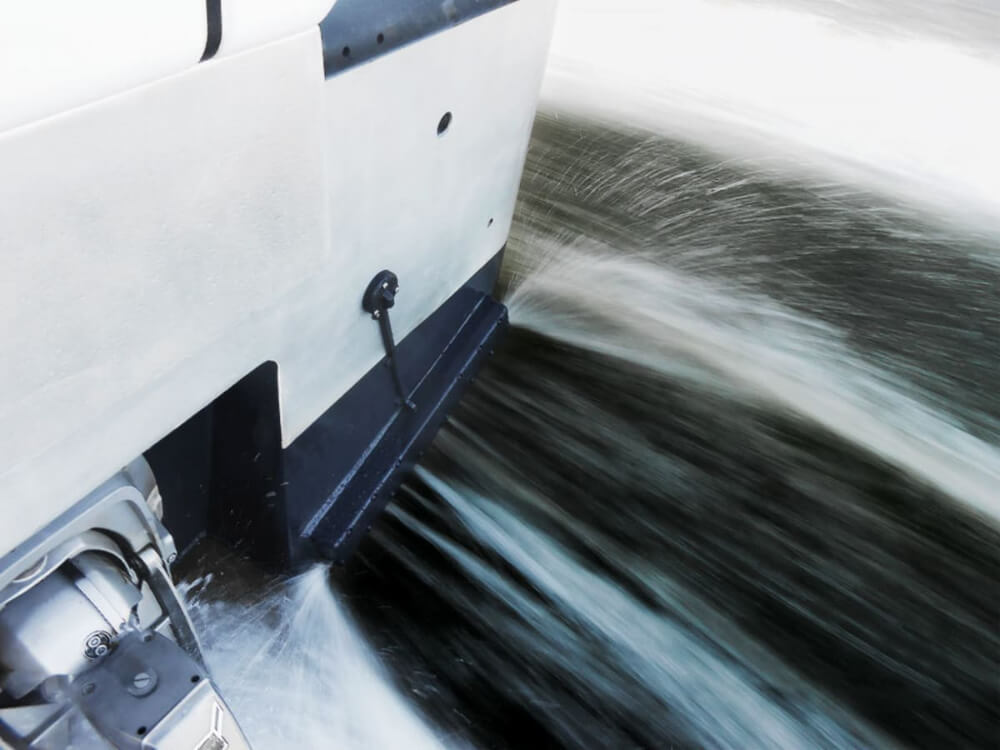

That means it is possible to fit a trim system over a propeller tunnel or partly over the chine, as the shape of the interceptor can follow almost any hull curvature. In difference from most trim tab designs, the interceptors are constructed out of composite materials. This means that you get a light construction that has almost zero added mass and it also leaves out all worries regarding corrosion problems and the need of zinc anodes.
Until recently interceptors have been traditional designed for larger vessels. Since 2001, when the Swedish company Humphree was formed, it has provided interceptor stabiliser systems for around 15,000 boats from 12m to 100m. However while the original Humphree series are offered in sizes from 350mm to 1500mm and various designs to fit hull shapes for boats from 12m to 200m+, they recently developed the X Series, a standardized interceptor for boats as small as 7.5m. This new X Series features all the same auto trim, auto list, co-ordinated turn and active rode control of the larger Humphree systems. They are available in five standard sizes; 300mm, 450mm, 600mm, 750mm and 900mm. Humphress are due to release a small boat series of interceptors later this
year.Another Swedish company, Zipwake also offers smaller units for trailer boats as well as larger cruisers. The Zipwake, Dynamic Trim Control System (DTCS) comes in four model sizes, suitable for planning and semi planning boats from 6m to 18m. One unique feature to Zipwake is they offer two alternatives for the cable through the transom, either above the waterline or concealed through the hull. The above waterline option is an important factor to consider when retrofitting the units to trailer boats with moulded or glassed in cockpit floors, making access difficult.