Different engine builders have different turbo-maintenance requirements, although whatever engine you have, chances are the turbo doesn’t need much looking after.
By Mike Smith
When was the last time you serviced your turbo? Maybe it’s time. Check your boost pressure to find out.
Turbocharged engines punch far above their weight, developing substantially more horsepower than naturally aspirated engines of similar displacement by pumping combustion air into the cylinders rather than relying on the engine to draw it in. This forces a greater volume of air, and therefore more oxygen, into each cylinder charge; more oxygen supports more fuel burn, and more fuel burn produces more power from the same cubic inches. Consequently, a smaller, lighter, more fuel-efficient turbo engine can replace a larger, heavier, natural motor with the same horsepower rating. And such weight savings can mean higher speed and/or less fuel consumption and, thanks to the physically smaller powerplant, more room for working in the engine compartment.
So, what’s the downside? Old-timers claim the higher power output of the turbo robs an engine’s lifespan versus a same-displacement natural — maybe it does, but few yachties put enough hours on their engines to find out for sure. For sure, it’s a consideration for commercial fishermen and round-the-world voyagers, many of whom prefer chunky, slow-turning naturally aspirated engines. But for the majority of skippers, the biggest turbo-related negative is that the darn thing is simply another component to break down, and it needs a little TLC once in a while. Nothing onerous, though.
Different engine builders have different turbo-maintenance requirements, although whatever engine you have, chances are the turbo doesn’t need much looking after: A new air filter every hundred hours or so, or maybe every year; an internal cleaning every couple of hundred hours, done without removing the turbo; and a rebuild after thousands of hours, usually more hours than you’ll put on your boat. All the recommendations for this stuff are in your engine’s owner’s manual — on the pages toward the back that you maybe didn’t read. Get your manual out and read those pages now.

How Does It Work?
Before you get totally engrossed, however, let’s take a minute and see what’s inside the turbocharger housing. A typical turbo has a shaft with a turbine wheel on one end (the “turbo”) and, in a separate compartment, a compressor wheel on the other (the “charger”). Exhaust gas passes through the turbine, setting it spinning. This spins the compressor, which pulls in combustion air through a filter, pressurizes (or “boosts”) it, and pumps it into the intake manifold, usually through an intercooler; turbochargers run hot, so cooling the intake air via an intercooler makes it pack more of a punch. Pretty simple, really.
Every turbocharger has a waste gate, basically a pressure-actuated port in the turbine housing that allows exhaust gas to exit directly without passing through the turbine. Without a waste gate, the boost pressure could rise high enough to damage the engine. When the boost pressure exceeds a pre-set limit, an actuator pushes on a connecting rod to open the waste gate; when the pressure drops, a spring inside the actuator closes the gate. A bypass valve does the same thing on the charger side, reducing excessive boost by diverting pressurized air back into the intake ahead of the turbo. (Some turbos have a blow-off valve that releases the excess pressure into the air.) If either the waste gate or the bypass valve sticks open, it will reduce turbo boost and engine performance will suffer. If either one sticks closed, it can damage the engine, maybe even kill it. Keeping the turbo clean will usually prevent such dire possibilities.
Traditional turbos use fixed turbine rotors; newfangled variable geometry turbos have movable turbine vanes that automatically adjust to match the exhaust gas flow. The vanes can be mechanically controlled by a pressure-sensitive actuator, similar to a conventional wastegate, or by an electronic control unit. Variable geometry turbos are more complex than conventional turbos, and difficult to rebuild, so most mechanics replace them, a costly repair. But whatever innards a turbocharger has, using a treatment to clean them of soot and other gunk is a major step toward preventing turbo issues.
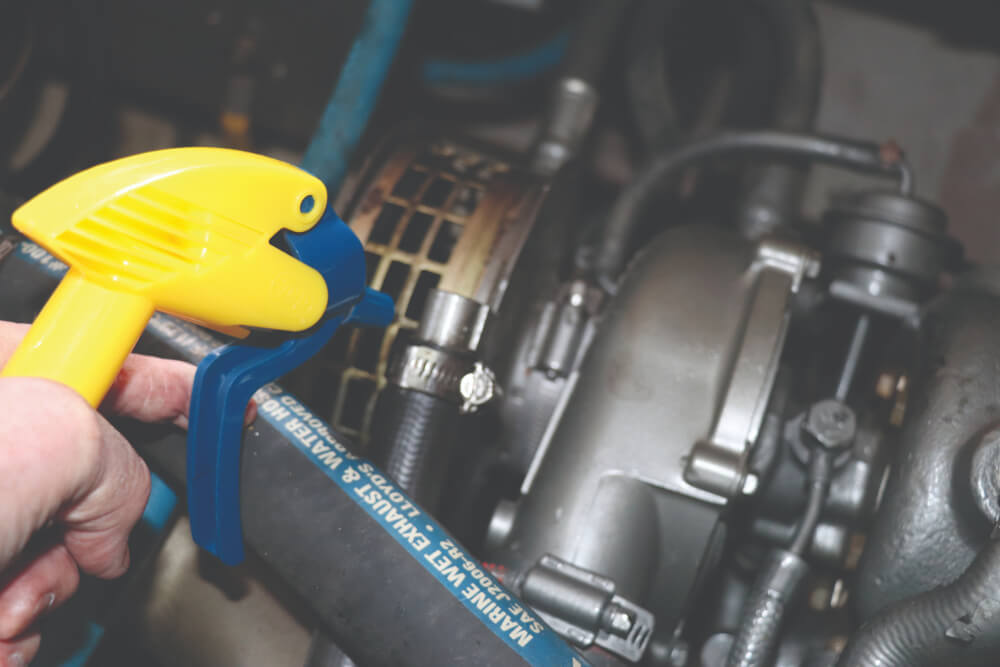
rinse it out
How do you know when your turbo needs attention? I asked Carl Schlemmer, a technical support specialist at Yanmar, and a guy who knows about all there is to know about turbochargers. Schlemmer says the most important tool when it comes to maintaining a turbo is a boost gauge. “When boost drops by 10 percent from normal, it’s time to clean the turbocharger,” he said, assuming nothing else is amiss onboard: The bottom’s not heavily fouled, the fuel and air filters are clean, etc.
But this means you have to know what normal boost is, so it’s important to keep a record of boost versus rpm, starting when the boat’s new, or at least when everything is just right. “Establish a baseline for boost pressure and use that as your standard.” (Some people just watch the exhaust, said Schlemmer, and while black exhaust can indicate turbo problems, it can also mean other things, like a dirty air filter.) And, he said, don’t forget the genset: Many of the larger models these days have turbo diesels under the sound shield
Actually, cleaning the turbo is straightforward: A wash agent is introduced via the air cleaner with the engine running, usually squirted or sprayed in short bursts from a spray bottle. It passes through the compressor side of the turbo, then into the engine’s intake manifold, through the cylinders, back through the turbo and out the exhaust, cleaning everything on its way. Some ship diesels have a wash tank permanently plumbed; you fill it with fresh water (yes, plain water), get the engine up to operating temperature and open a valve. The water’s sucked into the engine and blown out the exhaust. (A second cleaning system, for just the turbine, might also use water, or maybe crushed walnut shells or rice; they are cooked in the hot exhaust and blown out after scouring the turbine blades of soot and gunk.)
Yikes! What’s the deal with squirting water, or a water-based cleaner, into an engine? According to Schlemmer, the cleaner is introduced slowly, and in small amounts, with so much air that it just burns off without doing any harm. That assumes that the person squirting the cleaner into the air filter does so very slowly, with the engine running at the rpm specified in the manual. “Don’t dump a gallon of cleaner into the air filter all at once, or you’ll have some problems.” Schlemmer noted, further explaining that old Yanmar service manuals used to recommend cleaning your turbo under way, with the engine loaded, but now the recommendation is just for a particular rpm, specified in the manual, with the engine running in neutral. (Yanmar calls for at least 2500 rpm for cleaning the turbo blower on their 4JH80 engines, for example.) Some cleaners require rinsing with plain water after the cleaning cycle. Bottom line is, follow the directions.
What turbo cleaner is best? You’ll find a few in auto parts stores, but not all are suitable for diesel engines, so read the label. Or you can pay your mechanic to do the job; then if something goes south, it’s his fault.
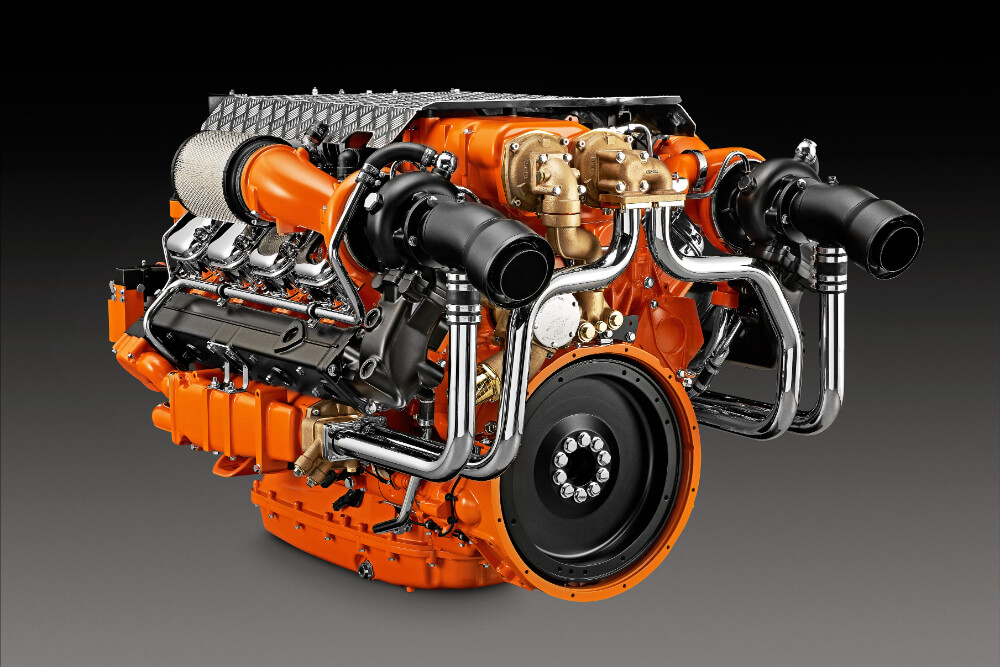
look inside and out
But what if, after enjoying a good wash, your turbo’s boost is still dropping? Start by pulling off the air filter to look at the fins on the compressor wheel, said Schlemmer. They should be sharp, almost like a knife, right to their tips. If not, if they’re rolled or otherwise damaged, don’t waste your money on more turbo wash — you need professional help. Rolled blades don’t pump as much air as they should and can cause an engine to overheat — too much fuel burning, not enough fresh air to cool the combustion chambers, and the engine’s cooling system can’t make up the difference. “If you’re having overheating problems that are unusual,” he said, “check your turbo.” While you have the air filter out, clean it or replace the element. Do this at least once a year.
Also, if you see oil in the turbo, call your mechanic. A turbo spins very fast — 40,000 or 50,000 rpm — and no-contact bearings (sometimes called labyrinth bearings) are used to reduce friction to almost nothing. No-contact bearings use a thin film of oil between the moving parts. This oil comes from the engine’s lube oil that also flows through the turbocharger – if the seal on a bearing fails, lube oil will leak into the turbo and eventually cause problems. This is also why you should let the engine idle for five minutes or so before shutting down. When the engine’s shut down abruptly, the oil pressure drops and the oil flow through the no-contact bearings stops just as abruptly— if the turbo’s still spinning fast from residual momentum, this can cause unnecessary wear on the bearings. What’s more, the hot turbo can actually bake whatever oil’s left in it, creating gunk you don’t want in there. Let the turbo slow down, and cool down, before shutting off the engine.
And one last thing. Once in a while remove your exhaust elbow and look into the turbine side of the turbo. (While the elbow’s off, check its innards for rust, too. It’s a good idea to do this yearly, although few people do.) The turbine might be coated with a thin layer of fine ash dust from the exhaust; vacuum it out, being careful not to damage the turbine blades. There shouldn’t be any oily clumps, rust or moisture, either — sometimes raw water from the exhaust elbow finds its way back into the turbine, where it causes problems. The turbine blades should be undamaged and fit tightly against the housing, with just enough clearance to let the turbine spin. Again, if something doesn’t look right, call a mechanic.
And remember. Anything beyond the problems we’ve just discussed should be left to a qualified pro, who can remove the turbo, take it into the shop, clean it thoroughly and, if necessary, rebuild it. Most turbos, however, live long, uneventful lives. Apply just a little TLC and your turbocharger should keep spinning into the future for many, many hours.

It's Not Always the Turbo
More turbo troubles result from outside sources, like saltwater leaks, than from mechanical failure, said Matthew Beer, general manager of SHM Dauntless Shipyard in Essex, CT (PMY’s home port). And sometimes, the problem is simply lack of exercise. To scout out an issue, start with a visual inspection, looking for oil or water leaks around the turbo, water dripping onto it, rust and so forth. Remove any insulating blankets so you can check underneath.
“Keep your engine clean and dry, and you can see drips easily,” said Beer. If there’s a minor issue, take care of it before it becomes major. (This is good advice for engines in general, not just turbos. If people spent more time in their engine rooms, they’d spend less time with their mechanics.)
For instance, Beer continued, one of his customers limped home with a malfunctioning engine whose turbocharger had seemingly crapped out. But when Beer checked, he found that saltwater had been dripping onto the actuator rod for the waste gate. When the customer throttled up to max rpm the actuator opened the waste gate, as it’s supposed to. But when he throttled back, rust on the rod prevented the gate from closing again. Beer fixed the problem by cleaning the rust off the actuator rod; there was nothing wrong with the turbo.
So, added Beer, if you have a turbo, make sure to use it. Run the engine to its rated rpm, maybe even a bit more, whenever you go out. “The biggest problem we see with turbochargers is people don’t use them,” said Beer.